Lāzermetināšana pret tradicionālo: Salīdzinošā analīze un perspektīvas
Lāzermetināšana pret tradicionālo: Salīdzinošā analīze un perspektīvas
Metināšanas metodes izvēle ir kritiski svarīga daudzām nozarēm, sākot no autobūves līdz medicīnai. Kamēr tradicionālās metināšanas metodes, piemēram, loka metināšana (MIG/MAG, TIG), joprojām ir plaši izplatītas, lāzermetināšana strauji iegūst popularitāti, pateicoties tās unikālajām priekšrocībām. Apskatīsim šo divu pieeju salīdzinošo analīzi un novērtēsim lāzermetināšanas attīstības perspektīvas.
Tradicionālās metināšanas metodes (loka metināšana)
Tradicionālā metināšana, īpaši loka metināšana, balstās uz elektriskā loka radīšanu starp elektrodu un sagatavi, kas ģenerē siltumu, kas nepieciešams metālu kausēšanai un savienošanai.
Priekšrocības:
Daudzpusība: Piemērota plašam metālu un biezumu diapazonam.
Relatīvi vienkārša aprīkojuma: Sākotnējais slieksnis darba uzsākšanai bieži ir zemāks.
Elastīgums: Iespēja veikt manuālu metināšanu grūti sasniedzamās vietās.
Zemas sākotnējās investīcijas: Aprīkojums parasti ir lētāks.
Trūkumi:
Augsta siltumievade: Izraisa lielas termiski ietekmētās zonas (TIA), deformācijas un atlikuma spriegumus.
Zema ātrums: Salīdzinot ar lāzermetināšanu, process var būt ievērojami lēnāks.
Nepieciešamība pēc papildmateriāliem: Bieži nepieciešami papildu materiāli šuves veidošanai.
Pēcapstrāde: Bieži nepieciešama šuves slīpēšana vai cita apstrāde tās platuma un nelīdzenumu dēļ.
Ietekme uz operatoru: Gāzu un dūmu izdalīšanās, kā arī intensīvs UV starojums.
Lāzermetināšana
Lāzermetināšana izmanto fokusētu lāzera staru ar augstu enerģijas blīvumu, lai kausētu un savienotu materiālus. Šī tehnoloģija nodrošina ļoti precīzu un koncentrētu siltumievadi.
Priekšrocības:
Minimāla siltumievade un maza TIA: Samazina deformācijas, atlikuma spriegumus un ļauj metināt termiski jutīgus materiālus.
Augsts metināšanas ātrums: Ievērojami pārspēj tradicionālās metodes, kas palielina produktivitāti.
Augsta šuves precizitāte un kvalitāte: Šaura, dziļa un gluda šuve, kas bieži neprasa pēcapstrādi.
Iespēja metināt dažādus materiālus: Ļauj savienot atšķirīgus metālus un sakausējumus.
Bezkontakta process: Mehāniskā kontakta trūkums ar sagatavi samazina instrumentu nodilumu.
Automatizācijas iespējas: Ideāli piemērota robotizētām sistēmām un augstas precizitātes masveida ražošanai.
Ekoloģiskums: Mazāk dūmu un gāzu salīdzinājumā ar loka metināšanu.
Trūkumi:
Augstas sākotnējās investīcijas: Lāzermetināšanas aprīkojums ir ievērojami dārgāks.
Sarežģīta uzstādīšana: Nepieciešams augsti kvalificēts personāls uzstādīšanai un kalibrēšanai.
Stingras prasības malu sagatavošanai: Nepieciešama augsta detaļu precizitāte.
Materiāla biezuma ierobežojumi: Ļoti bieziem materiāliem var būt nepieciešama daudzpakāpju metināšana vai hibrīdu metožu izmantošana.
Drošības prasības: Intensīvs lāzera starojums prasa stingrus drošības pasākumus un aizsardzību.
Salīdzinošā analīze
Lāzermetināšanas nākotne izskatās ļoti daudzsološa. Nepārtraukti attīstoties lāzertehnoloģijām (piemēram, šķiedru lāzeri kļūst jaudīgāki un pieejamāki), tās pielietojums tikai paplašināsies.
Galvenās tendences un perspektīvas:
Hibrīdmetināšana: Lāzermetināšanas un loka metināšanas kombinācija (piemēram, lāzera loka metināšana) apvieno abu metožu priekšrocības, nodrošinot augstu ātrumu un dziļu iespiešanos, saglabājot elastību.
Plānu materiālu lāzermetināšana un mikrometināšana: Precizitātes palielināšana ļauj strādāt ar ultra-plāniem materiāliem un mikroelektronikā.
Aditīvā ražošana: Lāzermetināšana ir galvenais elements dažās metālu 3D drukas tehnoloģijās, piemēram, tiešā lāzera nogulsnēšana (DED).
Robotikas un MI attīstība: Lāzermetināšanas integrācija ar progresīviem robotiem un mākslīgā intelekta sistēmām ļaus izveidot pilnībā autonomus un adaptīvus metināšanas kompleksus.
Energoefektivitāte: Jaunās paaudzes lāzeri kļūst energoefektīvāki, kas samazina ekspluatācijas izmaksas.
Jaudi spēka palielināšana: Lāzeru jaudas pieaugums ļaus metināt biezākus materiālus, saglabājot augstu ātrumu un kvalitāti.
Lāzermetināšana, lai gan prasa augstākas sākotnējās investīcijas, piedāvā ievērojamas priekšrocības precizitātē, ātrumā un kvalitātē, padarot to par vēlamo izvēli augsto tehnoloģiju ražošanā. Ilgtermiņā, ņemot vērā aprīkojuma izmaksu samazināšanos un turpmāku tehnoloģiju attīstību, tai būs arvien dominējošāka loma mūsdienu rūpniecībā.
Viedās rūpnīcas: Kā Industrija 4.0 maina ražošanu
Viedās rūpnīcas: Kā Industrija 4.0 maina ražošanu?
Industrija 4.0 jeb Ceturtā industriālā revolūcija ir fundamentālas pārmaiņas ražošanas vidē, ko raksturo padziļināta digitālo tehnoloģiju integrācija. Tās centrālais elements ir "viedās rūpnīcas" (Smart Factories) — ražošanas sistēmas, kur mašīnas, aprīkojums, produkti un cilvēki mijiedarbojas reāllaikā, veidojot pašorganizējošu un pašoptimizējošu vidi.
Kas ir Industrija 4.0 un viedās rūpnīcas?
Industrija 4.0 ir koncepcija, kas apraksta ražošanas procesu digitalizāciju un automatizāciju, izmantojot progresīvas tehnoloģijas. Mērķis ir radīt savstarpēji savienotas, inteliģentas ekosistēmas, kas spēj mācīties, pielāgoties un ieviest jauninājumus.
Viedās rūpnīcas ir ražošanas objekti, kas aprīkoti ar savienotām mašīnām, automatizētām sistēmām un datu vadītiem procesiem. Tie palielina efektivitāti un samazina cilvēku kļūdas, veidojot elastīgas, pašorganizējošas sistēmas.
Industrijas 4.0 galvenās tehnoloģijas
Ražošanas transformācija Industrijas 4.0 ietvaros balstās uz vairākām galvenajām tehnoloģijām:
Lietu internets (IoT): Ļauj mašīnām, ierīcēm un sistēmām apmainīties ar datiem reāllaikā, vācot informāciju par aprīkojuma stāvokli un optimizējot procesus.
Mākslīgais intelekts (MI) un mašīnmācīšanās: Tiek izmantoti lielu datu apjomu analīzei, likumsakarību noteikšanai, bojājumu prognozēšanai, procesu automatizācijai un lēmumu pieņemšanai reāllaikā.
Lielie dati un analītika: Milzīgu datu apjomu vākšana un analīze ļauj atklāt slēptās likumsakarības, optimizēt loģistiku, samazināt izmaksas un uzlabot produktu kvalitāti.
Mākoņdatošana: Nodrošina mērogojamu infrastruktūru datu glabāšanai un apstrādei, nodrošinot nepārtrauktu saziņu starp mašīnām, cilvēkiem un sistēmām.
Industriālā robotika un automatizācija: Roboti pārņem atkārtotus un bīstamus uzdevumus, palielinot produktivitāti, samazinot kļūdu skaitu un nodrošinot diennakts produkcijas izlaidi.
Kiberfiziskās sistēmas: Integrē skaitļošanas un fiziskos komponentus, ļaujot fiziskiem procesiem mijiedarboties ar digitālajām sistēmām.
Kā Industrija 4.0 maina ražošanu?
Industrijas 4.0 ieviešana rada būtiskas izmaiņas ražošanas sektorā:
Efektivitātes un produktivitātes paaugstināšana: Uzdevumu automatizācija, darba procesu optimizācija un atkritumu samazināšana ievērojami palielina ražošanu ar mazākiem resursu patēriņiem.
Kvalitātes kontroles uzlabošana: MI un datu analīzes sistēmas nodrošina nepārtrauktu kvalitātes monitoringu un kontroli katrā ražošanas posmā, samazinot defektus un uzlabojot produktu konsekvenci.
Prognostiskā apkope: Sensori un analītika ļauj prognozēt aprīkojuma bojājumus pirms to rašanās, samazinot dīkstāves laiku un remonta izmaksas.
Izmaksu samazināšana: Procesu optimizācija, efektīva resursu izmantošana, atkritumu samazināšana un prediktīvā apkope veicina operatīvo izdevumu samazināšanos.
Paaugstināta elastība un pielāgošana: Viedās rūpnīcas var ātri pielāgoties pieprasījuma izmaiņām, ražojot personalizētus produktus lielā apjomā ar minimālām papildu izmaksām.
Uzlabota drošība un darba apstākļi: Bīstamu uzdevumu automatizācija un sensoru izmantošana darba vides monitoringam samazina negadījumu un traumu risku.
Ilgtspējība un videi draudzīgums: Industrijas 4.0 tehnoloģijas ļauj optimizēt enerģijas patēriņu, samazināt emisijas un atkritumus, veicinot pāreju uz ilgtspējīgāku ražošanu.
Nākotnes perspektīvas
Industrija 4.0 turpina attīstīties, un jau parādās Industrijas 5.0 koncepcijas, kas koncentrējas uz ciešāku sadarbību starp cilvēkiem un mašīnām. MI, visticamāk, spēlēs vēl nozīmīgāku lomu šajā pārmaiņā, nodrošinot ne tikai automatizāciju, bet arī inteliģentu mijiedarbību, kur mašīnas un cilvēki strādā plecu pie pleca, lai sasniegtu kopīgus mērķus.
Robotizētu sistēmu izmantošana metāla konstrukciju ražošanā: Nākotne ir klāt
Robotizētu sistēmu izmantošana metāla konstrukciju ražošanā: Nākotne ir klāt
Metāla konstrukciju ražošana, kas tradicionāli asociējas ar smagu fizisku darbu un sarežģītām manuālām operācijām, piedzīvo īstu revolūciju, pateicoties robotizētu sistēmu ieviešanai. Šīs modernās tehnoloģijas ne tikai automatizē procesus; tās transformē visu nozari, paaugstinot precizitāti, drošību un efektivitāti.
Kāpēc roboti metālapstrādē?
Mūsdienu pasaulē konkurence liek uzņēmumiem meklēt jaunus veidus, kā optimizēt ražošanu. Robotizācija metāla konstrukciju ražošanā piedāvā risinājumu daudzām galvenajām problēmām:
Precizitātes un kvalitātes paaugstināšana: Roboti veic atkārtotus uzdevumus ar neticamu precizitāti un stabilitāti, samazinot cilvēkfaktoru un defektus. Tas ir īpaši svarīgi metināšanai, griešanai un liekšanai, kur novirzes var radīt nopietnas problēmas.
Produktivitātes palielināšana: Roboti var strādāt visu diennakti, bez pārtraukumiem un noguruma, ievērojami saīsinot ražošanas cikla laiku.
Darba apstākļu un drošības uzlabošana: Cilvēka izslēgšana no bīstamām un monotonām operācijām, piemēram, metināšanas neērtās pozās, darba ar smagām sagatavēm vai augstā temperatūrā, samazina traumu un arodslimību risku.
Ražošanas izmaksu samazināšana: Neskatoties uz sākotnējām investīcijām, robotizētās sistēmas atmaksājas, samazinot brāķi, ietaupot materiālus, samazinot darbaspēka vajadzības un paaugstinot kopējo efektivitāti.
Ražošanas elastība: Mūsdienu robotus ir viegli pārprogrammēt dažādu uzdevumu veikšanai un darbam ar dažāda veida izstrādājumiem, kas ļauj ātri pielāgoties mainīgajām tirgus prasībām.
Galvenās robotu pielietošanas jomas
Robotizētās sistēmas plaši tiek izmantotas dažādos metāla konstrukciju ražošanas posmos:
Robotizēta metināšana: Tas, iespējams, ir visizplatītākais pielietojums. Metināšanas roboti nodrošina stabilu šuves kvalitāti, lielu metināšanas ātrumu un iespēju strādāt ar grūti pieejamām vietām. Tie var veikt gan loka, gan lāzermetināšanu, nodrošinot ideālus savienojumus atbildīgām konstrukcijām.
Robotizēta griešana: Lāzera, plazmas vai hidroabrazīvā griešana, izmantojot robotus, ļauj sasniegt augstu precizitāti sarežģītu formu metāla griešanai, samazinot atkritumus un vajadzību pēc turpmākas apstrādes.
Liekšana un formēšana: Roboti tiek integrēti ar lokšņu locīšanas presēm un citām formēšanas mašīnām, automatizējot sagatavju padevi un pozicionēšanu, kas palielina liekšanas ātrumu un precizitāti.
Virsmas apstrāde: Roboti tiek izmantoti metāla konstrukciju slīpēšanai, pulēšanai, šuvju tīrīšanai un krāsošanai, nodrošinot vienmērīgu pārklājumu un augstu virsmas kvalitāti.
Iekraušanas un izkraušanas operācijas: Smagie rūpnieciskie roboti ir neaizstājami lielgabarīta un smagu metāla sagatavju pārvietošanai, kas paaugstina drošību un samazina personāla fizisko slodzi.
Kvalitātes kontrole: Roboti, kas aprīkoti ar mašīnredzes sistēmām un 3D skeneriem, var automātiski pārbaudīt ģeometriskos parametrus, defektu esamību un metināto šuvju kvalitāti, nodrošinot stingru kontroli katrā ražošanas posmā.
Izaicinājumi un perspektīvas
Robotizētu sistēmu ieviešana nav bez izaicinājumiem. Tas ietver ievērojamas sākotnējās investīcijas, nepieciešamību pārkvalificēt personālu (no operatoriem līdz inženieriem-programmētājiem), kā arī jaunu sistēmu integrācijas sarežģītību ar esošo aprīkojumu.
Tomēr perspektīvas, ko paver robotizācija, atsver šīs grūtības. Attīstoties mākslīgajam intelektam un mašīnmācībai, roboti kļūst vēl gudrāki, spējīgi pielāgoties un pašmācīties. Paplašinās kolaboratīvo robotu (kobotu) pielietojums, kas var droši strādāt plecu pie pleca ar cilvēku, veicot rutīnas vai bīstamus uzdevumus.
Metāla konstrukciju ražošana virzās uz pilnībā automatizētām un intelektuālām rūpnīcām, kur roboti spēlēs centrālu lomu, nodrošinot vēl nepieredzētu efektivitātes, precizitātes un drošības līmeni. Uzņēmumi, kas pirmie apgūs šīs tehnoloģijas, iegūs ievērojamu konkurences priekšrocību tirgū.
Pielietojums piedevu tehnoloģijās (3D drukā) metālapstrādē: jauns ražošanas laikmets
Pielietojums piedevu tehnoloģijās (3D drukā) metālapstrādē: jauns ražošanas laikmets
Piedevu tehnoloģijas jeb 3D druka, kas reiz šķita zinātniskā fantastika, šodien pārveido daudzas nozares, un metālapstrāde nav izņēmums. No prototipu veidošanas līdz sarežģītu funkcionālu detaļu ražošanai, metāla 3D druka paver vēl nepieredzētas iespējas, papildinot un dažos gadījumos aizstājot tradicionālās apstrādes metodes.
Kas ir piedevu tehnoloģijas metālapstrādē?
Atšķirībā no tradicionālās (subtraktīvās) metālapstrādes, kur materiāls tiek noņemts, lai iegūtu vēlamo formu, piedevu tehnoloģijas veido objektus slāni pa slānim, pievienojot materiālu. Metāliem tas visbiežāk notiek, izmantojot pulverveida metālus un jaudīgus enerģijas avotus, piemēram, lāzerus vai elektronu starus, kas sakausē pulvera daļiņas kopā.
Galvenās metāla 3D drukāšanas metodes ietver:
Selektīvā lāzersinterēšana/kausēšana (SLS/SLM): Lāzers selektīvi kausē vai saķepina metāla pulveri slāni pa slānim.
Tiešā lāzera metāla uzklāšana (DED): Metāla pulveris tiek padots fokusētā lāzera starā, kas to kausē, veidojot slāni pa slānim.
Līmvielas strūklas druka (Binder Jetting): Līmviela tiek uzklāta uz metāla pulvera slāņiem, veidojot detaļu, kas pēc tam tiek saķepināta krāsnī.
Materiāla ekstrūzija (Material Extrusion – Bound Metal Deposition): Līdzīgi FDM polimēru drukāšanai, bet izmanto metāla pulveri, kas sajaukts ar saistvielu, ar sekojošu saķepināšanu.
3D drukas priekšrocības metālapstrādei
Piedevu tehnoloģiju pielietošana metālapstrādē sniedz vairākas būtiskas priekšrocības:
Sarežģīta ģeometrija un dizaina optimizācija: Spēja radīt detaļas ar neticami sarežģītu iekšējo struktūru, piemēram, režģa konstrukcijām, dzesēšanas kanāliem vai dobām formām. Tas ļauj optimizēt detaļas svaru, uzlabot tās funkcionālās īpašības (piemēram, siltuma apmaiņu) un radīt pielāgotus produktus.
Prototipu izstrādes laika un izmaksu samazināšana: Ātra funkcionālo prototipu izgatavošana tieši no 3D modeļa ievērojami paātrina produktu izstrādes ciklus un samazina aprīkojuma izmaksas.
Materiālu atkritumu samazināšana: Atšķirībā no subtraktīvajām metodēm, kur lielākā daļa materiāla var pārvērsties skaidiņās, piedevu procesi rada ievērojami mazāk atkritumu, kas ir īpaši izdevīgi, strādājot ar dārgiem un retiem metāliem.
Ražošana pēc pieprasījuma un pielāgošana: Iespēja ražot unikālas vai mazas sērijas detaļas bez dārgas iekārtu pārkonfigurācijas. Tas ir ideāli piemērots specializētu instrumentu, medicīnisko implantu vai novecojušu iekārtu rezerves daļu radīšanai.
Detaļu remonts un atjaunošana: Dažus piedevu procesus, piemēram, DED, var izmantot, lai palielinātu materiālu uz bojātām metāla detaļām, atjaunojot to funkcionalitāti un pagarinot kalpošanas laiku.
Pielietojuma jomas
Piedevu tehnoloģijas jau tiek aktīvi izmantotas dažādās metālapstrādes nozarēs:
Aviācijas un kosmosa rūpniecība: Vieglu, izturīgu un sarežģītu komponentu ražošana lidmašīnām un kosmosa kuģiem (piemēram, turbīnu lāpstiņas, kronšteini).
Medicīna: Individuālu implantu (piemēram, locītavu protēžu, galvaskausa plākšņu), ķirurģisko instrumentu un zobārstniecības konstrukciju veidošana.
Automobiļu rūpniecība: Prototipu, sporta automašīnu funkcionālo detaļu, kā arī instrumentu un aprīkojuma ražošana.
Enerģētika: Komponentu izgatavošana gāzes turbīnām, siltummaiņiem un citiem elementiem, kas darbojas ekstremālos apstākļos.
Instrumentu ražošana: Presformu ar integrētiem dzesēšanas kanāliem izgatavošana liešanai ar spiedienu, kas samazina cikla laiku un uzlabo produkta kvalitāti.
Izaicinājumi un nākotne
Neskatoties uz visām priekšrocībām, piedevu tehnoloģijas metālapstrādē saskaras ar vairākiem izaicinājumiem:
Augstas iekārtu un materiālu izmaksas: Investīcijas rūpnieciskajos metāla 3D printeros un specializētajos pulveros joprojām ir ievērojamas.
Ražošanas ātrums: Liela apjoma sērijveida ražošanā piedevu procesi joprojām var būt lēnāki salīdzinājumā ar tradicionālajām metodēm.
Virsmas kvalitāte un pēcapstrāde: Ar 3D druku iegūtām detaļām bieži nepieciešama papildu mehāniskā apstrāde, lai sasniegtu nepieciešamo virsmas tīrību un precizitāti.
Standartizācija un kvalifikācija: Nozaru standartu izstrāde un personāla kvalifikācija darbam ar šīm sarežģītajām tehnoloģijām joprojām notiek.
Tomēr nepārtraukta pētniecība un attīstība, iekārtu un materiālu izmaksu samazināšanās, kā arī jaunu, ātrāku un precīzāku drukas metožu parādīšanās liecina, ka piedevu tehnoloģijas spēlēs arvien nozīmīgāku lomu metālapstrādes nākotnē, paverot durvis inovācijām un ražošanas transformācijai.
Tendences CNC darbgaldu attīstībā augstas precizitātes metālapstrādei
Tendences CNC darbgaldu attīstībā augstas precizitātes metālapstrādei
Pasaulē, kur precizitāte un efektivitāte ir galvenie veiksmes faktori, ciparu vadības (CNC) darbgaldi joprojām ir augstas precizitātes metālapstrādes sirds. Šīs iekārtas nepārtraukti attīstās, pielāgojoties jaunām nozares prasībām un piedāvājot nepārspējamas iespējas sarežģītu un augstas kvalitātes detaļu radīšanai. Apskatīsim galvenās tendences, kas veido šīs svarīgās nozares nākotni.
1. Viedā automatizācija un integrācija ar robotiku
Mūsdienu CNC darbgaldi pārsniedz vienkāršu programmu izpildi. Tie kļūst par integrētu automatizētu sistēmu daļu. Roboti arvien biežāk tiek izmantoti automātiskai sagatavju iekraušanai un izkraušanai, instrumentu maiņai un pat pēcapstrādei, samazinot cilvēka iejaukšanos un palielinot produktivitāti. Tas ir īpaši svarīgi sērijveida ražošanai, kur atkārtojamība un ātrums ir kritiski.
2. Paplašinātas daudzasu apstrādes iespējas
Darbgaldi ar 5, 7 un vairāk asīm vairs nav retums, bet kļūst par standartu augstas precizitātes metālapstrādē. Šīs iekārtas ļauj apstrādāt sarežģītas ģeometrijas detaļas vienā iestatījumā, samazinot ražošanas laiku, novēršot kļūdas, kas saistītas ar pāriestatīšanu, un ievērojami uzlabojot precizitāti. Spēja apstrādāt detaļas dažādos leņķos paver durvis inovatīvu formu radīšanai, kas iepriekš nebija sasniedzamas.
3. Industrijas 4.0 un IIoT (Rūpnieciskais lietu internets) integrācija
CNC darbgaldu pievienošana kopējam ražošanas tīklam, izmantojot IIoT, nav tikai tendence, bet gan nepieciešamība. Tas ļauj reāllaikā uzraudzīt iekārtu darbību, vākt datus par produktivitāti, prognozēt atteices un veikt prognozējošu apkopi. Šāda pieeja ievērojami palielina efektivitāti, samazina dīkstāves laiku un optimizē resursu izmantošanu. Darbgaldu digitālie dvīņi ļauj modelēt procesus un optimizēt programmas pirms reālās apstrādes uzsākšanas.
4. Hibrīdās tehnoloģijas: subtraktīvās un aditīvās ražošanas simbioze
Viena no aizraujošākajām tendencēm ir hibrīdo darbgaldu parādīšanās, kas apvieno tradicionālo subtraktīvo (materiāla noņemšana) un aditīvo (materiāla pieaudzēšana, 3D druka) apstrādi. Tas paver jaunus horizontus sarežģītu iekšējo struktūru detaļu radīšanai, samazina atkritumu daudzumu un ļauj remontēt bojātas dārgas sastāvdaļas. Piemēram, var izdrukāt detaļas pamatni un pēc tam precīzi apstrādāt tās virsmas.
5. Paaugstināta energoefektivitāte un ekoloģiskums
Pieaugot uzmanībai ilgtspējīgai attīstībai, CNC darbgaldu ražotāji aktīvi strādā pie savu mašīnu enerģijas patēriņa samazināšanas. Energoefektīvāku dzinēju, dzesēšanas sistēmu un programmatūras izmantošana, kas optimizē instrumenta trajektorijas, palīdz samazināt oglekļa pēdas nospiedumu un ekspluatācijas izmaksas. Tāpat vērojama pāreja uz videi draudzīgākām griešanas šķidruma un atkritumu utilizācijas sistēmām.
6. Mākslīgais intelekts (MI) un mašīnmācīšanās vadībā
MI un mašīnmācīšanās sāk spēlēt svarīgu lomu apstrādes procesu optimizēšanā. Šīs tehnoloģijas tiek izmantotas automātiskai griešanas režīmu pielāgošanai mainīgajiem apstākļiem, instrumenta nolietojuma prognozēšanai, anomāliju atklāšanai un pat optimālu instrumenta trajektoriju ģenerēšanai. Tas nodrošina stabilāku darbību, uzlabotu virsmas kvalitāti un ilgāku instrumenta kalpošanas laiku.
Secinājums
CNC darbgaldu attīstības tendences augstas precizitātes metālapstrādei norāda uz nākotni, kurā mašīnas būs vēl gudrākas, autonomākas un universālākas. Uzņēmumiem, kas vēlas saglabāt konkurētspēju, ir ļoti svarīgi sekot šīm inovācijām un integrēt tās savos ražošanas procesos. Investīcijas progresīvās CNC tehnoloģijās ir investīcijas precizitātē, produktivitātē un ilgtspējīgā attīstībā.
Augstas entropijas sakausējumu detaļu apstrāde: izaicinājumi un iespējas
Augstas entropijas sakausējumu detaļu apstrāde: izaicinājumi un iespējas
Ievads
Augstas entropijas sakausējumi (AES) ir jauna metālu klase, kas satur vismaz piecus galvenos elementus aptuveni vienādās proporcijās. Tiem raksturīga augsta izturība, cietība, karstumizturība un izturība pret koroziju, kas padara tos īpaši piemērotus aviācijai, enerģētikai un aizsardzības nozarei.
Tomēr AES apstrāde ar griešanas metodēm rada ievērojamus izaicinājumus – to sarežģītais sastāvs un fizikālās īpašības veicina instrumenta nodilumu un pieprasa īpašus tehnoloģiskus risinājumus.
Galvenās apstrādes grūtības
1. Augsta cietība un izturība
Vairumam AES cietība pārsniedz 400–500 HV, bet izturība – 1000 MPa. Tas izraisa paaugstinātas griešanas slodzes un ātru instrumenta nolietošanos.
2. Zema siltumvadītspēja
Siltums uzkrājas griešanas zonā, pārkarsējot gan detaļu, gan instrumentu. Nepieciešama efektīva dzesēšana.
3. Anizotropija un mikrostrukturāla neviendabība
Dažos AES sastopamas mainīgas cietības zonas, kas rada vibrācijas un samazina virsmas kvalitāti.
Risinājumi un iespējas
Instrumenta izvēle
-
Karbīda griezēji ar nanosegumiem (TiAlN, AlCrN)
-
Keramikas un CBN plāksnītes gala apstrādei
-
DLC pārklājumi mīkstākiem sakausējumiem
Griešanas režīmi
-
Samazinātas padeves un ātrumi (par 20–40% zemāki)
-
Sekli griezumi ar stabilām trajektorijām
Dzesēšana
-
Augstspiediena dzesēšana vai MQL
-
Dažkārt – sausā apstrāde ar piemērotu instrumentu
Salīdzinājums ar citiem materiāliem
Materiāls | Apstrādes kvalitāte | Piezīmes |
---|---|---|
Titāns (augstas izturības) | ★★☆☆☆ | Liela cietība, slikta siltumvadītspēja |
Nerūsējošais tērauds 316 | ★★★☆☆ | Apmierinošs ar dzesēšanu |
Inconel (Ni sakausējums) | ★☆☆☆☆ | Augsts instrumenta nodilums |
AES (piem. CoCrFeMnNi) | ★★☆☆☆ | Nepieciešama individuāla pieeja |
Nākotnes perspektīvas
AES potenciāls kļūst arvien nozīmīgāks smagās rūpniecības pielietojumos. Lai tos efektīvi izmantotu, jāattīsta:
-
Specializēti instrumentu materiāli un segumi
-
Precīzā apstrāde ar procesu monitoringu
-
Hibrīdtehnoloģijas (piemēram, lāzera apstrāde kombinācijā ar frēzēšanu)
Secinājums
AES apstrāde ir izaicinoša, taču ar pareizu pieeju to iespējams realizēt efektīvi. Tehnoloģiskās inovācijas ļauj šos augsti izturīgos materiālus izmantot arī praktiskā ražošanā.
Nanopārklājumi griezējinstrumentiem: izturība un nodilumizturība
Nanopārklājumi griezējinstrumentiem: izturība un nodilumizturība
Ievads
-
Mūsdienu metālapstrādei nepieciešama augsta precizitāte un stabilitāte
-
Asmeņu nodilums izraisa dīkstāves un detaļu brāķi
-
Risinājums: nanopārklājumi, kas būtiski pagarina instrumenta kalpošanas laiku
Kas ir nanopārklājumi?
-
Ļoti plāni (līdz desmitiem nanometru) daudzslāņu pārklājumi
-
Veidoti no nitrīdiem, karbīdiem, oksīdiem (PVD vai CVD metodes)
-
Līdz 7 slāņiem, katrs zem 100 nm
Nanopārklājumu priekšrocības
-
Lielāka nodilumizturība
-
Mazāks berzes koeficients
-
Noturība agresīvā vidē (ķīmija, karstums)
-
Instrumenta kalpošanas laiks x2–x5
Nanopārklājumu veidi
Pārklājums | Sastāvs | Īpašības |
---|---|---|
TiAlN | Titāna-alumīnija nitrīds | Universāls, karstumizturīgs |
AlTiN | Al vairāk nekā Ti | Lielam ātrumam |
CrN | Hroma nitrīds | Laba izturība pret koroziju |
DLC | Dimanta tipa ogleklis | Zema berze, ideāli krāsainiem metāliem |
nACo® | TiAlN/Si₃N₄ nanokompozīts | Izturīgs pret karstumu un nodilumu |
Uzklāšanas tehnoloģijas
-
PVD — zema temperatūra, videi draudzīgs
-
CVD — labāk lieliem instrumentiem
-
Jaunumi: HiPIMS, ALD, nanoslāņu laminēšana
Piemēri
-
TiAlN: kalpošanas ilgums +300% nerūsējošam tēraudam
-
DLC: ideāli alumīnijam un varam
-
Inconel-718 apstrāde: lielāka padeve, mazāk vibrāciju
Pārklājuma izvēle
Sagataves materiāls | Ieteicamais pārklājums |
---|---|
Oglekļa tērauds | TiAlN, AlTiN |
Titāns un sakausējumi | nACo, AlTiN |
Varš, alumīnijs | DLC, CrN |
Karstumizturīgi sakausējumi | nACo, daudzslāņu AlTiN |
Nākotne
-
Pašatjaunojoši pārklājumi
-
Gudrie pārklājumi, kas reaģē uz slodzi
-
Kombinētie pārklājumi (PVD + ALD)
-
Nano-berzes kontrole
Secinājums
-
Nanopārklājumi samazina izmaksas un uzlabo procesa kvalitāti
-
Pareizs pārklājums = ilgāks darbs, mazāk bojājumu
-
Nākotne — ilgtspējīgi, adaptīvi risinājumi
Videi draudzīgi griešanas šķidrumi: augu izcelsmes eļļu alternatīvas
Videi draudzīgi griešanas šķidrumi: augu izcelsmes eļļu alternatīvas
Ievads
-
Griešanas šķidrumi ir būtiski metālapstrādē
-
Parastie šķidrumi ir kaitīgi videi un veselībai
-
Rūpniecība virzās uz ilgtspējīgām tehnoloģijām
Kāpēc augu izcelsmes šķidrumi?
-
Izgatavoti no sojas, rapša, saulespuķu vai palmu eļļām
-
Bioloģiski noārdāmi, netoksiski
-
Samazina izmaksas par atkritumu apsaimniekošanu
Augu izcelsmes griešanas šķidrumu veidi
-
Tīras augu eļļas
-
Vienkāršas, bet oksidējas un ir ar īsu glabāšanas laiku
-
-
Emulgējamie biošķidrumi
-
Sajaukti ar ūdeni labākai dzesēšanai
-
-
Sintētiski taukskābju esteri
-
Ilgnoturīgāki un karstumizturīgāki
-
Salīdzinājums
Parametrs | Minerāleļļas | Biošķidrumi |
---|---|---|
Ietekme uz vidi | Augsta | Zema |
Iegādes cena | Zemāka | Augstāka, bet atmaksājas |
Instrumentu kalpošana | Vidēja | Garāka |
Utilizācija | Jāattīra | Noārdāmi dabā |
Izaicinājumi
-
Augstākas sākotnējās izmaksas
-
Nepieciešama iekārtu pielāgošana
-
Uzglabāšanas apstākļu jūtība
Piemēri
-
Audi un Bosch izmanto rapša eļļas šķidrumus
-
DMG Mori piedāvā iekārtas ar bio-SOŽ atbalstu
-
Mazie Skandināvijas uzņēmumi pāriet uz biošķidrumiem
Nākotnes tendences
-
Universālu bioformulu izstrāde
-
pH un mikrobioloģijas monitorings
-
Slēgtās aprites sistēmas
Secinājums
-
Biošķidrumi ir efektīva un videi draudzīga alternatīva
-
Ilgtspējīgi risinājumi kļūst arvien izdevīgāki
Top 10 Ultraskaņas un precīzās CNC apstrādes iekārtas
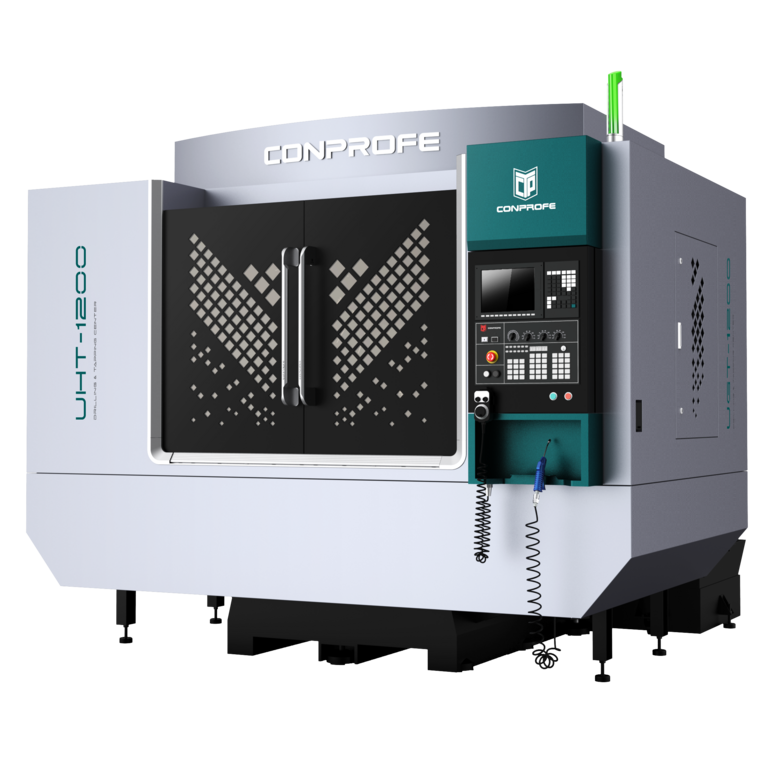
Top 10 Ultraskaņas un precīzās CNC apstrādes iekārtas
1. DAMA.ch ultraskaņas mikroapstrādes sistēmas
Šveice
Eksperti ultraprecīzā ultraskaņas apstrādē mikrokomponentiem – optika, MEMS, keramika, stikls. Nodrošina nanometru virsmas kvalitāti un submikronu precizitāti.
2. Conprofe ultraskaņas CNC centri (ULM sērija)
Ķīna
3 un 5 asu CNC centri ar 16–60 kHz ultraskaņas vibrācijām. Paredzēti cietu un trauslu materiālu apstrādei – safīrs, keramika, stikls, oglekļa šķiedra. Videi draudzīgas un efektīvas iekārtas.
3. DMG MORI Ultrasonic / LASERTEC sērija
Vācija / Japāna
5 asu ultraskaņas apstrādes centri ar augstu precizitāti un automatizācijas iespējām – piemēroti medicīnai, aviācijai un optikai.
4. Yamazaki Mazak (Variaxis & Integrex)
Japāna
Daudzfunkcionālas CNC iekārtas ar augstu precizitāti un termālo stabilitāti.
5. Makino PS / T sērija
Japāna
Ātrdarbīgas iekārtas formu un aviācijas detaļu apstrādei ar augstu atkārtojamību.
6. GF Machining Solutions (Mikron, AgieCharmilles)
Šveice
Eksperti mikroapstrādē un EDM – izmantots medicīnā, pulksteņu un elektronikas industrijā.
7. Okuma MB & Multus
Japāna
Robustas un uzticamas CNC iekārtas ar termisko kompensāciju – ideāli sarežģītu detaļu apstrādei.
8. FANUC Robodrill + automatizācija
Japāna
Kompaktas, efektīvas iekārtas ar iespēju integrēt ultraskaņas instrumentus un robotus.
9. Starrag (NB / LX / STC)
Šveice
Specializēti 5 asu centri turbīnām un aviācijas konstrukcijām ar augstu precizitāti.
10. Mandelli Sistemi SPARK
Itālija
Horizontālās CNC iekārtas ar augstu stingrību – piemērotas auto un aviācijas nozarēm.
Kā automatizēt sagatavju ielādi: risinājumi mazām darbnīcām
Kā automatizēt sagatavju ielādi: risinājumi mazām darbnīcām
Mazajos un vidējos ražošanas uzņēmumos automatizācija bieži tiek uzskatīta par dārgu vai nepieejamu. Taču viena no laikietilpīgākajām operācijām — sagatavju ielāde un izlāde — jau šodien ir automatizējama bez milzīgām investīcijām. Mūsdienīgi risinājumi palīdz paaugstināt produktivitāti un samazināt iekārtu nolietojumu, pat ierobežotos budžetos un telpās.
Kāpēc automatizēt sagatavju ielādi
Rokas ielādes problēmas:
-
Cilvēku kļūdas un nogurums
-
Pārtraukumi, dīkstāves un nestabila padeve
-
Ierobežots cikla ātrums
-
Nekonsekventa kvalitāte
Automatizācijas priekšrocības:
-
Stabils darba ritms
-
Mazāk kļūdu un brāķa
-
Iespēja strādāt daļēji automātiski vai bez operatora
-
Labāka atdeve no iekārtām
-
Mazākas darbaspēka izmaksas
Risinājumu varianti mazajiem uzņēmumiem
1. Gravitācijas un vibrācijas padevēji
Vienkāršas ierīces mazu detaļu padevei (piemēram, skrūvēm).
-
Padeve caur bunkuru un šļūteni
-
Der sērijveida ražošanai
-
Cena: €500–€2,000
2. Pneimopiedziņas padeves sistēmas
-
Der vidēja izmēra sagatavēm
-
Vienkārša uzbūve, mazs enerģijas patēriņš
-
Iespējama integrācija vecākās iekārtās
3. Manipulatori un kolaboratīvie roboti (coboti)
-
Piemēroti detaļu ielādei/izņemšanai un šķirošanai
-
Droši darbam blakus cilvēkiem
-
Sākot no €12,000
-
Piemēroti maztirāžas ražošanai
4. Lineārās portālsistēmas
-
Kompakti mehānismi virs iekārtām
-
Efektīvi vienveidīgām darbībām
-
Aizņem maz vietas
-
Viegli pielāgojami
5. Automātiskās karuseļa sistēmas un paletēšanas galdi
-
Sagataves tiek iepriekš uzkrautas paletēs
-
Sistēma pati padod tās apstrādei
-
Nodrošina nepārtrauktu darbu
Kā izvēlēties piemērotāko risinājumu
Jautājums | Kas jāņem vērā |
---|---|
Sagatavju tips un izmērs | Svars, forma, izmēri |
Ražošanas apjoms | Viengabala, maza vai vidēja sērija |
Telpas iespējas | Iekārtu izvietojums un pieejamība |
Budžets | Vai iespējama pakāpeniska ieviešana? |
Elastība | Vai bieži jāmaina detaļu veidi? |
Ieviešanas soļi
-
Analizējiet esošās darbības
-
Izvēlieties pilotprojektu
-
Piemeklējiet tehniski piemērotu risinājumu
-
Nodrošiniet drošību
-
Apmāciet darbiniekus
-
Salīdziniet rezultātus pirms un pēc
Prakses piemērs
Frēzēšanas darbnīca ar trim CNC iekārtām un diviem operatoriem zaudēja daudz laika uz manuālu ielādi.
Risinājums:
Uzstādīts zemas cenas robots ar dubulto tvērēju.
Rezultāts:
-
Produktivitāte pieauga par 28%
-
Brāķis samazinājās par 14%
-
Ieguldījums atmaksājās 9 mēnešos
Secinājums
Sagatavju ielādes automatizācija ir efektīvs solis pat mazajiem uzņēmumiem. Pieejamie risinājumi kļūst kompaktāki un pieejamāki, ļaujot spert pirmo soli ceļā uz gudrāku ražošanu.
IIoT integrācija metālapstrādē: priekšrocības un pirmie soļi
IIoT integrācija metālapstrādē: priekšrocības un pirmie soļi
Digitālās pārveides laikmetā ražošanas uzņēmumi arvien biežāk ievieš IIoT (Industrial Internet of Things – Rūpnieciskais lietu internets) tehnoloģijas. Īpaši perspektīva joma ir metālapstrāde, kur svarīga ir efektivitāte, uzticamība un precizitāte.
Kas ir IIoT un kāpēc tas nepieciešams metālapstrādē?
IIoT savieno sensoriem un programmām aprīkotus rūpnieciskus iekārtas, kas savstarpēji apmainās ar datiem reāllaikā. Tas ļauj:
-
uzraudzīt iekārtas 24/7,
-
prognozēt bojājumus,
-
optimizēt darba grafikus,
-
analizēt ražošanas procesus.
Piemērs:
CNC iekārta nosūta datus par vārpstas temperatūru, vibrācijām un cikla laiku uz mākoni. Sistēma paziņo tehniķim, ja parādās anomālijas — pirms notiek bojājums.
Galvenās priekšrocības
-
Mazāki dīkstāves laiki
-
Lielāka ražība
-
Resursu ekonomija
-
Datu pārredzamība
-
Labāka kvalitāte
Pirmie soļi IIoT ieviešanā
-
Veiciet iekārtu un vajadzību auditu
-
Noteiciet prioritātes — kādi dati ir svarīgākie
-
Uzstādiet sensorus, uzsāciet datu vākšanu
-
Izvēlieties platformu (piemēram, MindSphere)
-
Apmāciet personālu
-
Palaidiet pilotprojektu
Ko var automatizēt jau šodien
-
CNC uzraudzību
-
Trauksmes par vibrācijām un pārkaršanu
-
Dīkstāves uzskaiti
-
Instrumenta nodiluma analīzi
-
Kvalitātes kontroli reāllaikā
Secinājums
IIoT ir šodienas iespēja. Sāciet ar vienu iekārtu un soli pa solim virzieties uz digitālu ražotni.
Kā pareizi apkalpot un kalibrēt lāzera sistēmas, lai nodrošinātu griezuma precizitāti
Kā pareizi apkalpot un kalibrēt lāzera sistēmas, lai nodrošinātu griezuma precizitāti
Ievads
Lāzera griešanas iekārtas nodrošina augstu precizitāti, taču tikai tad, ja tās tiek regulāri apkalpotas un kalibrētas. Netīrumi, vibrācijas un nepareiza fokusācija var būtiski ietekmēt rezultātu. Profilaktiskā apkope ir obligāta.
1. Kāpēc apkope ir svarīga
Slikta apkope izraisa:
-
Neprecīzus griezumus un atkritumus;
-
Optikas un mehānisko daļu nolietošanos;
-
Pārkaršanas un drošības riskus;
-
Augstas remonta izmaksas un dīkstāvi.
2. Ikdienas darbi
-
Tīriet lēcas un spoguļus ar izopropilspirtu un bezšķiedru salvetēm.
-
Pārbaudiet fokusu ar lineālu vai autofokusa funkciju.
-
Pārbaudiet dzesēšanas sistēmu – šķidruma līmeni un noplūdes.
-
Noņemiet putekļus no griešanas zonas un ventilācijas.
3. Nedēļas un mēneša uzdevumi
Reizi nedēļā:
-
Pievelciet stiprinājumus, pārbaudiet spoguļu stāvokli.
-
Tīriet ventilācijas filtru un ventilatorus.
-
Pārbaudiet siksnas un kustības gludumu.
Reizi mēnesī:
-
Kalibrējiet X un Y asis.
-
Nomainiet nodilušos optikas elementus.
-
Testējiet lāzera stara simetriju.
4. Kalibrēšanas soļi
-
Stara ceļa kalibrācija: izšaujiet impulsus stūra punktos.
-
Fokusa testi: grieziet līnijas dažādos augstumos.
-
Asu kalibrācija: grieziet režģi vai apli un pārbaudiet izmērus.
-
Programmatūras kalibrācija: regulējiet motora soļus uz mm, kompensāciju.
5. Biežākās kļūdas
Kļūda | Sekas |
---|---|
Tīrīšana ar pirkstiem/papīru | Skrāpējumi, karsēšana |
Dzesēšanas sistēmas ignorēšana | Pārkaršana, bojājumi |
Nav kalibrācijas pēc pārvietošanas | Griešanas neprecizitāte |
6. Drošības noteikumi
-
Vienmēr atslēdziet iekārtu pirms apkopes.
-
Izmantojiet aizsargbrilles un cimdi.
-
Glabājiet optiku sausā, tīrā vidē.
Kā izvēlēties optimālo dzesēšanas sistēmu CNC iekārtām
Kā izvēlēties optimālo dzesēšanas sistēmu CNC iekārtām
Augstas precizitātes apstrādē siltums ir viens no galvenajiem faktoriem. Pārkaršana var radīt instrumentu bojājumus, detaļas deformāciju un apstrādes nestabilitāti. Tāpēc pareiza dzesēšanas sistēma ir būtiska ilgtspējīgai un kvalitatīvai CNC darbībai.
Šajā rakstā apskatīsim dažādas dzesēšanas sistēmas, to plusus, mīnusus un piemērotību atkarībā no materiāla un ražošanas apstākļiem.
Kāpēc dzesēšana ir svarīga?
Siltums apstrādes laikā izraisa:
-
Instrumentu nodilumu
-
Dimensiju neprecizitāti
-
Virsmas kvalitātes pasliktināšanos
-
Mikroplaisas un detaļas deformāciju
Efektīva dzesēšana samazina berzi, noņem siltumu un palīdz atbrīvot skaidas.
Galvenie dzesēšanas veidi
1. Šķidrā dzesēšana (emulsija, eļļa)
Visbiežāk izmantotā metode — šķidrums tiek pievadīts griešanas zonai.
Priekšrocības:
-
Efektīvi dzesē un samazina berzi
-
Uzlabo skaidu izvadīšanu
-
Samazina instrumentu nodilumu
Trūkumi:
-
Nepieciešama filtrācija un uzturēšana
-
Var izraisīt koroziju
-
Ietekme uz vidi
Ieteicams:
Tērauds, titāns, niķeļa sakausējumi, smagas un dziļas apstrādes gadījumos.
2. Minimālā eļļošanas sistēma (MQL)
Mazs daudzums smērvielas tiek izsmidzināts aerosolā uz griešanas vietu.
Priekšrocības:
-
Tīra darba vide
-
Mazs dzesēšanas šķidruma patēriņš
-
Videi draudzīgāka
Trūkumi:
-
Nepietiekama dzesēšana pie augstas slodzes
-
Prasa precīzu uzstādīšanu
Ieteicams:
Alumīnijs, plastmasa, mīkstie sakausējumi, kad nepieciešams samazināt apkopes laiku.
3. Gaisa dzesēšana (saspiests gaiss)
Saspiests gaiss tiek novirzīts uz apstrādes zonu.
Priekšrocības:
-
Nav nepieciešams dzesēšanas šķidrums
-
Mazs apkope
-
Viegli ieviest
Trūkumi:
-
Zema dzesēšanas efektivitāte
-
Nav piemērots cietiem materiāliem
Ieteicams:
Plastmasas, grafīts, mīksti metāli, viegla apstrāde.
4. Kriogēnā dzesēšana (šķidrais slāpeklis, CO₂)
Zema temperatūra tieši griešanas zonā.
Priekšrocības:
-
Maksimāli pagarina instrumentu kalpošanu
-
Lieliska virsmas kvalitāte
-
Videi neitrāla
Trūkumi:
-
Augstas izmaksas
-
Nepieciešama īpaša uzglabāšana un aprīkojums
Ieteicams:
Niķeļa sakausējumi, aviācijas un medicīnas detaļas, augstas intensitātes frēzēšana.
Kā izvēlēties?
Materiāls:
-
Titāns, tērauds — šķidrums vai kriogēnā
-
Alumīnijs — MQL
-
Plastmasa — gaiss
Apstrādes slodze:
-
Intensīva — nepieciešama efektīva dzesēšana
-
Vieglā apstrāde — pietiek ar minimālu
Vides un ekspluatācijas faktori:
-
Pieejamas dzesēšanas filtrācijas sistēmas?
-
Vai nepieciešama tīra vide (piem., medicīna)?
Budžets un ilgtspēja:
-
MQL samazina izdevumus
-
Kriogēnā dzesēšana — augsta efektivitāte, bet dārga
Secinājums
Nav universālas dzesēšanas sistēmas — tās izvēle jābalsta uz materiālu, uzdevumu un ražošanas iespējām. UDBU palīdzēs izvēlēties piemērotāko risinājumu jūsu ražošanai.
Sazinieties ar mums, lai uzlabotu CNC efektivitāti.
Jauno materiālu apstrādes apskats: no kompozītiem līdz augstas stiprības sakausējumiem
Jauno materiālu apstrādes apskats: no kompozītiem līdz augstas stiprības sakausējumiem
Mūsdienu ražošanā arvien biežāk tiek izmantoti jauni materiāli, kas apvieno zemu svaru ar augstu izturību un ķīmisko noturību. Taču šo materiālu apstrāde uz CNC iekārtām prasa precīzu pieeju — sākot no instrumenta izvēles līdz dzesēšanas sistēmām.
Šajā rakstā aplūkojam biežāk sastopamos modernās apstrādes materiālus, to īpašības, priekšrocības un apstrādes nianses.
Oglekļa šķiedras kompozīts (karbons)
Priekšrocības:
-
Ļoti viegls un izturīgs
-
Izturīgs pret koroziju
-
Samazina vibrācijas
Apstrādes izaicinājumi:
-
Instrumentu strauja nodilšana
-
Risks materiāla slāņošanai
-
Nepieciešama augsta apgriezienu precizitāte
Ieteikumi:
-
Lietot dimanta pārklājuma instrumentus (PCD)
-
Uzstādīt putekļu nosūkšanas sistēmas
-
Samazināt griešanas spēkus un vibrācijas
Titāna sakausējums (piem., Ti-6Al-4V)
Priekšrocības:
-
Augsta izturība un ķīmiskā stabilitāte
-
Mazs svars, bet stiprs kā tērauds
-
Labi piemērots medicīnai un aviācijai
Apstrādes izaicinājumi:
-
Zema siltumvadītspēja — pārkaršanas risks
-
Materiāla uzkrāšanās uz griezējmalas
-
Augsta materiāla cena
Ieteikumi:
-
Izmantot karbīda instrumentus ar TiAlN vai AlCrN pārklājumu
-
Pielietot augstspiediena dzesēšanu
-
Samazināt padevi, saglabāt mērenu ātrumu
Niķeļa super sakausējumi (Inconel, Hastelloy, Waspaloy)
Priekšrocības:
-
Izturīgi ļoti augstās temperatūrās
-
Izcila ķīmiskā noturība
-
Forma nemainās pie augstas slodzes
Apstrādes izaicinājumi:
-
Augstas griešanas slodzes
-
Strauja instrumenta nodilšana
-
Tendence uz sacietēšanu
Ieteikumi:
-
Lietot nodilumizturīgus karbīda instrumentus
-
Pastāvīgi uzraudzīt instrumenta stāvokli
-
Apstrādāt ar mazāku griešanas dziļumu
Augstas stiprības alumīnija sakausējumi (7xxx sērija)
Priekšrocības:
-
Zems svars un liela stiprība
-
Laba apstrāde un oksidēšanas spēja
-
Plaši izmantots aviācijā un auto industrijā
Apstrādes izaicinājumi:
-
Skaidas uzkrāšanās
-
Atbiras un uzmavas veidošanās
Ieteikumi:
-
Izmantot frēzes ar pulētām kanālēm
-
Augsti apgriezieni un zema padeve
-
Sausā vai MQL dzesēšana
Inženiertehniskie plastmasas materiāli (PEEK, PTFE, Delrin)
Priekšrocības:
-
Ļoti viegli un ķīmiski izturīgi
-
Elektriski izolējoši
-
Viegli apstrādājami
Apstrādes izaicinājumi:
-
Deformācija no karstuma
-
Garas, lipīgas skaidas
-
Zema stingrība
Ieteikumi:
-
Lietot vienzobu, ļoti asus instrumentus
-
Augsta vārpstas ātrums, zema padeve
-
Izvairīties no materiāla pārkaršanas
Secinājums
Mūsdienu materiāli paver jaunas iespējas, bet prasa rūpīgu pieeju. UDBU piedāvā risinājumus un atbalstu visos soļos — no instrumenta izvēles līdz parametru optimizācijai.
Sazinieties ar mums, lai uzlabotu savu CNC apstrādes efektivitāti.
Detalizēta automatizācija CNC iekārtām: kā paaugstināt ražošanas efektivitāti
Detalizēta automatizācija CNC iekārtām: kā paaugstināt ražošanas efektivitāti
Mūsdienu ražošanā svarīga ir ātruma, precizitātes un stabilitātes kombinācija. Automatizēta detaļu ielāde un izlāde CNC iekārtās ir ceļš uz efektivitāti un konkurētspēju.
Kāpēc automatizēt?
Rokas darbs ir laikietilpīgs un pakļauts kļūdām:
-
Operators pieļauj kļūdas noguruma dēļ
-
Iekārtas stāv dīkstāvē, kamēr tiek apkalpotas
-
Paaugstināts nelaimes gadījumu risks
Automatizācija šo problēmu novērš — darbs tiek veikts ātrāk, drošāk un precīzāk.
Kādas sistēmas tiek izmantotas?
1. Robotizētie manipulatori
-
6 asu industriālie roboti — sarežģītiem uzdevumiem
-
Portāla roboti — smagām un lielām detaļām
-
Sadarbības roboti (coboti) — droši, viegli programmējami, piemēroti mazajiem uzņēmumiem
2. Konveijeri
-
Rullīšu — lieliem, plakaniem izstrādājumiem
-
Lentes — universālam pielietojumam
-
Moduļu ar šķirošanu — dažāda veida detaļām
Integrācija ar CNC
Nepieciešami:
-
Datu apmaiņas interfeisi (OPC UA, Ethernet/IP)
-
Savietojami CNC kontrolieri
-
Drošības sistēmas: barjeras, apvalki, stop pogas
Loģiku iespējams pārvaldīt caur PLC vai CNC programmu.
Automatizācijas priekšrocības:
-
Mazāk darbaspēka izmaksu
-
Lielāka ražošana (līdz 50%)
-
Stabils, kvalitatīvs rezultāts
-
Nepārtraukta darbība 24/7
-
Drošāka un ergonomiskāka vide
Piemēri praksē:
-
Alumīnija detaļas — roboti palielināja ražību par 40%
-
Mazsēriju ražošana — coboti ļāva strādāt bez operatora nakts maiņās
Secinājums:
Automatizācija nav sarežģīta — īpaši, ja sadarbojaties ar UDBU. Mēs palīdzēsim izvēlēties un ieviest piemērotāko risinājumu.
Sazinieties ar mums jau šodien!
Lāzers vai aukstā zāģis cauruļu griešanai — ko izvēlēties?
Lāzers vai aukstā zāģis cauruļu griešanai — ko izvēlēties?
Izvēloties cauruļu griešanas aprīkojumu, jāņem vērā daudzi faktori: precizitāte, ātrums, izmaksas, materiāla tips utt. Salīdzināsim divas populāras metodes — lāzera griešanu un aukstā zāģa griešanu, lai palīdzētu jums izdarīt pareizo izvēli.
Lāzera griešana
Priekšrocības:
-
Ļoti augsta precizitāte un griezuma kvalitāte. Gluds griezums bez atbēruma; bieži nav nepieciešama pēcapstrāde.
-
Elastība. Iespējams griezt sarežģītas formas un caurumus.
-
Automatizācija. Mūsdienīgas iekārtas viegli integrējas ražošanas līnijās.
Trūkumi:
-
Augstas iekārtas un apkalpošanas izmaksas.
-
Mazāk efektīva biezsienu cauruļu griešanai.
-
Nepieciešamas kvalificētas zināšanas.
Ideāli piemērota: precīzai, maza apjoma griešanai no nerūsējošā tērauda, alumīnija, vara un citiem krāsainiem metāliem.
Aukstā zāģa griešana
Priekšrocības:
-
Zemas izmaksas. Pieejamāks risinājums.
-
Labi piemērota biezsienu caurulēm.
-
Vienkārša apkope un lietošana.
Trūkumi:
-
Ierobežotas formas — galvenokārt taisni griezumi.
-
Zemāka precizitāte. Var būt nepieciešama pēcapstrāde.
-
Trokšņaināka, vairāk atkritumu.
Ideāli piemērota: masveida ražošanai, melno metālu griešanai, vienkāršām taisnām operācijām.
Salīdzinošā tabula:
Parametrs | Lāzera griešana | Aukstā zāģa griešana |
---|---|---|
Precizitāte | Ļoti augsta | Vidēja |
Ātrums | Vidējs | Augsts (taisniem griezumiem) |
Iekārtas izmaksas | Augstas | Vidējas/Zemas |
Sarežģītas formas | Jā | Nē |
Apkope | Sarežģīta/Dārga | Vienkārša |
Secinājums
Ja prioritāte ir precizitāte un daudzpusība, izvēlieties lāzeru. Ja svarīgas ir zemas izmaksas un ātra griešana, aukstais zāģis būs piemērotāks.
Nepieciešama palīdzība ar aprīkojuma izvēli? Sazinieties ar mūsu komandu — palīdzēsim atrast labāko risinājumu jūsu vajadzībām.
CNC virpas darbības optimizēšana: padomi lielākai precizitātei un efektivitātei
CNC virpas darbības optimizēšana: padomi lielākai precizitātei un efektivitātei
Mūsdienu ražošanas pasaulē CNC (datorvadības) virpas ir būtisks aprīkojums, kas nodrošina augstu precizitāti un atkārtojamību. Tomēr pat vismodernākās iekārtas prasa pareizu apkopi, konfigurāciju un darba plūsmas organizāciju, lai sasniegtu maksimālu veiktspēju. Šajā rakstā sniedzam praktiskus padomus, kā optimizēt jūsu CNC virpas darbību, lai uzlabotu gan precizitāti, gan efektivitāti.
1. Regulāra iekārtas apkope
Pareiza un regulāra apkope ir viens no būtiskākajiem faktoriem, kas ietekmē CNC virpas darbību.
-
Pārbaudiet eļļošanas sistēmas darbību un līmeņus.
-
Attīriet vadotnes un darba virsmas no skaidas un putekļiem.
-
Veiciet vārpstu un ratiņu pārbaudi attiecībā uz nodilumu vai vibrāciju.
2. Instrumentu kalibrācija
Nepareiza instrumentu pozicionēšana var novest pie kļūdām gala izstrādājumā. Veiciet regulāru:
-
Instrumentu kalibrēšanu un atkārtotu iestatīšanu.
-
Asmens stāvokļa un nolietojuma pārbaudi.
-
Automātisko instrumentu nomainītāju pārbaudi, ja tāds ir pieejams.
3. Programmatūras un G-koda optimizācija
Efektīvs G-kods var ievērojami saīsināt apstrādes laiku un samazināt kļūdu risku.
-
Pārskatiet trajektorijas, lai izvairītos no liekas kustības.
-
Izmantojiet CAM programmatūras optimizācijas funkcijas.
-
Ieviesiet adaptīvo griešanu sarežģītiem materiāliem.
4. Darba materiāla sagatavošana
Nesagatavoti vai neprecīzi nostiprināti materiāli var radīt problēmas apstrādes laikā.
-
Pārliecinieties, ka sagatave ir pareizi nostiprināta.
-
Izvēlieties piemērotu materiāla turētāju vai čoku.
-
Pārbaudiet sagataves izmēru un formu pirms apstrādes.
5. Datu uzraudzība un analīze
Mūsdienu CNC iekārtas bieži piedāvā monitoringa funkcijas, kas ļauj analizēt darbības efektivitāti.
-
Izmantojiet datus, lai novērtētu cikla laiku un instrumentu nolietojumu.
-
Identificējiet vājās vietas darbplūsmā.
-
Ieviesiet uzlabojumus, pamatojoties uz reālo veiktspēju.
Secinājums
CNC virpas ir efektīvas tikai tik ilgi, cik labi tās tiek uzturētas un vadītas. Ar pareizu pieeju, kvalitatīviem instrumentiem un regulāru apkopi iespējams ievērojami uzlabot ražošanas kvalitāti, ātrumu un uzticamību. Optimizējiet savu darbību jau šodien, un rezultāti nebūs ilgi jāgaida.
Vai jums ir nepieciešama jauna vai modernizēta CNC virpa? Apskatiet mūsu iekārtu klāstu šeit
Kā izvēlēties piemērotāko CNC programmatūru jūsu ražošanas vajadzībām
Kā izvēlēties piemērotāko CNC programmatūru jūsu ražošanas vajadzībām
CNC (Computer Numerical Control) tehnoloģija ir kļuvusi par neatņemamu daļu no modernās ražošanas. Taču veiksmīgai darbībai ar CNC iekārtām nepieciešama ne tikai augstas kvalitātes aparatūra, bet arī piemērota programmatūra, kas atbilst jūsu uzņēmuma specifikai. Šajā rakstā apskatīsim, kā izvēlēties vispiemērotāko CNC programmatūru jūsu vajadzībām.
1. Izprotiet savas ražošanas vajadzības
Pirms izvēlaties programmatūru, ir svarīgi saprast:
-
Kādu materiālu jūs apstrādājat (koks, metāls, plastmasa u.c.)
-
Kāda veida CNC iekārtas jums ir (frēze, lāzers, plazma, virpa u.c.)
-
Cik sarežģītus darbus veicat (vienkārši izgriezumi vai sarežģītas 3D formas)
-
Cik liela ir jūsu ražošanas jauda (individuāls, sērijveida vai masveida pasūtījums)
2. Galvenie CNC programmatūras veidi
Programmatūras veids | Funkcija |
---|---|
CAD (Computer-Aided Design) | Zīmējumu un dizainu veidošana |
CAM (Computer-Aided Manufacturing) | Ģenerē ceļu instrumentiem, balstoties uz CAD modeļiem |
G-code redaktori / Simulācijas rīki | Ļauj pārskatīt un optimizēt kodu pirms reālas apstrādes |
Daži rīki apvieno vairākas funkcijas vienā platformā.
3. Populāras CNC programmatūras iespējas
-
Fusion 360 – apvieno CAD un CAM, ļoti piemērots prototipēšanai un mazam ražošanas apjomam
-
SolidWorks + SolidCAM – lieliski piemērots sarežģītai 3D apstrādei
-
Vectric (VCarve, Aspire) – lielisks rīks kokapstrādei, intuitīva saskarne
-
Mach3 / Mach4 – kontrolē CNC iekārtas, vienkāršs interfeiss, piemērots hobijiem un mazām darbnīcām
-
SheetCAM – labi piemērots plazmas, lāzera un liesmas griešanai
4. Ko ņemt vērā izvēloties?
- Lietošanas ērtums – cik ātri darbinieki apgūs programmu
- Savietojamība ar jūsu iekārtām – vai tā darbojas ar jūsu CNC kontrolleri
- Atbalsts un dokumentācija – vai ir pieejami mācību materiāli, tehniskais atbalsts
- Cena un licences nosacījumi – izvērtējiet vienreizējās, abonēšanas vai bezmaksas iespējas
- Programmas attīstība – vai programmatūra tiek regulāri atjaunināta
5. Nākotnes perspektīva: automatizācija un mākoņtehnoloģijas
Modernās CNC programmas bieži piedāvā:
-
Mākoņkrātuvi dizainiem
-
Automatizētu darbplūsmu
-
Integrāciju ar ERP un loģistikas sistēmām
-
Datu analītiku par darba efektivitāti
Šādas iespējas ir īpaši svarīgas uzņēmumiem, kas plāno paplašināties vai optimizēt ražošanu.
Secinājums
CNC programmatūras izvēle ir būtisks solis ceļā uz efektīvu, precīzu un rentablu ražošanu. Neatkarīgi no tā, vai esat hobija meistars vai rūpniecības uzņēmums, piemērota programmatūra palīdzēs jums maksimāli izmantot jūsu iekārtu potenciālu.
💬 Padoms: Pirms iegādes pārbaudiet programmatūras demo versiju vai izmēģinājuma periodu, lai pārliecinātos, ka tā atbilst jūsu vajadzībām.
Stabilitātes nodrošināšana augstas ātruma lāzergriešanā: no griešanas stratēģijas līdz sadursmju novēršanai
Stabilitātes nodrošināšana augstas ātruma lāzergriešanā: no griešanas stratēģijas līdz sadursmju novēršanai
Augstas ātruma lāzergriešana nodrošina nepārspējamu precizitāti un efektivitāti metālapstrādē. Tomēr, lai sasniegtu optimālu veiktspēju, nepieciešama stratēģiska pieeja, kas ietver gan griešanas plānošanu, gan modernu sadursmju novēršanas tehnoloģiju izmantošanu.
Griešanas stratēģijas
-
Kontūru analīze: Pirms griešanas novērtē materiāla ģeometriju, lai identificētu potenciālos nestabilos apgabalus.
-
Secība: Plāno griešanas kārtību tā, lai samazinātu lāzera galvas kustību pāri jau izgrieztiem laukumiem.
-
Iesākuma un beigu ceļi: Izstrādā tā, lai izvairītos no svarīgu apgabalu šķērsošanas.
-
Simulācijas izmantošana: Lieto CAM programmatūru, lai simulētu procesu un identificētu problēmas pirms faktiskās griešanas.
Modernas sadursmju novēršanas tehnoloģijas
-
ICA (Intelligent Collision Avoidance) no Lantek: Nodrošina mikrogriezumus nestabilās zonās, lai novērstu detaļu pārvietošanos.
-
Aktīvā sadursmju novēršana no Precitonix: Automātiski pielāgo Z asi, lai izvairītos no šķēršļiem.
-
Lāzera attāluma sensori no Wenglor: Precīzi mēra attālumus, lai izvairītos no sadursmēm automatizētās sistēmās.
-
Mašīnredze un mākslīgais intelekts: Reāllaikā analizē un koriģē procesu, lai novērstu novirzes.
Apkope un kalibrēšana
-
Regulāras pārbaudes un kalibrēšana ir būtiskas, lai nodrošinātu iekārtu darbspēju un precizitāti.
-
Programmatūras atjauninājumi sniedz jaunākās sadursmju novēršanas iespējas.
Priekšrocības
-
Lielāks ražošanas apjoms
-
Mazākas izmaksas
-
Lielāka drošība
-
Augstāka gala produkta kvalitāte
Kā izvēlēties kompresoru lāzera vai plazmas griezējam: kritēriji un padomi
Kā izvēlēties kompresoru lāzera vai plazmas griezējam: kritēriji un padomi
Izmantojot lāzera vai plazmas iekārtas, būtiska loma ir ne tikai pašam griešanas instrumentam, bet arī palīgiekārtām – piemēram, kompresoram. Tās veiktspēja un kvalitāte ietekmē griešanas stabilitāti, griezuma tīrību un iekārtas kalpošanas ilgumu.
Šajā rakstā apskatīsim, kā pareizi izvēlēties kompresoru lāzera vai plazmas griezējam, kam pievērst uzmanību un kādas īpašības ir vissvarīgākās.
Kāpēc nepieciešams kompresors lāzera un plazmas griešanā?
Kompresors piegādā saspiestu gaisu, kas pilda vairākas funkcijas:
-
Izvada dūmus un izkausētās daļiņas no griešanas zonas;
-
Dzesē apstrādes zonu, samazinot slodzi uz instrumentu;
-
Aizsargā optiku (lāzera gadījumā) no piesārņojuma;
-
Veido plazmu (augstspiediena plazmas griešanā).
Gaisa padeves stabilitāte un kvalitāte tieši ietekmē darba precizitāti.
Galvenie izvēles kritēriji
1. Gaisa plūsma (l/min vai m³/h)
Plūsmas apjomam jāatbilst vai jābūt nedaudz lielākam par iekārtas prasībām:
-
Plazmas griešanai: 200–500 l/min;
-
Lāzeriem: 50–300 l/min.
Ņem vērā:
-
Spiediena zudumus caurulēs;
-
Nepārtrauktu darbību;
-
Iespējamus nākotnes paplašinājumus.
2. Izvades spiediens (bāri/MPa)
-
Lāzeriem: 5–7 bāri;
-
Plazmas iekārtām: 6–8 bāri un vairāk.
Izvēlies kompresoru ar drošu rezervi.
3. Gaisa kvalitāte
Īpaši svarīga lāzera griešanā:
-
Lieto filtrus un mitruma atdalītājus;
-
Kritiskām vajadzībām – gaisa žāvētāju.
4. Kompresora veids
-
Vārpstas kompresori – lētāki, skaļāki, nolietojas ātrāk;
-
Skrūvju kompresori – dārgāki, klusi, piemēroti ilgai darbībai.
5. Gaisa tvertne (resīvers)
Jo lielāks tilpums, jo stabilāka padeve:
-
Plazmai: 50–200 litri;
-
Lāzeriem: 30–100 litri.
Papildu padomi
-
Pievērs uzmanību trokšņu līmenim;
-
Veic regulāru apkopi;
-
Pārbaudi elektropadevi (220V vai 380V);
-
Iekļauj jaudas rezervi – vismaz 20%.
Noslēgumā
Pareizi izvēlēts kompresors nodrošina darba kvalitāti un aizsargā jūsu iekārtu. Nepieciešams izvērtēt vajadzības un izvēlēties piemērotāko risinājumu.