Lazerinis Suvirinimas Prieš Tradicinį: Lyginamoji Analizė ir Perspektyvos
Lazerinis Suvirinimas Prieš Tradicinį: Lyginamoji Analizė ir Perspektyvos
Suvirinimo metodo pasirinkimas yra kritiškai svarbus daugeliui pramonės šakų, nuo automobilių gamybos iki medicinos. Nors tradiciniai suvirinimo metodai, tokie kaip lankinis suvirinimas (MIG/MAG, TIG), išlieka plačiai paplitę, lazerinis suvirinimas sparčiai populiarėja dėl savo unikalių privalumų. Panagrinėkime šių dviejų metodų lyginamąją analizę ir įvertinkime lazerinio suvirinimo plėtros perspektyvas.
Tradiciniai suvirinimo metodai (lankinis suvirinimas)
Tradicinis suvirinimas, ypač lankinis, grindžiamas elektros lanko sukūrimu tarp elektrodo ir ruošinio, kuris generuoja šilumą, būtiną metalams lydyti ir sujungti.
Privalumai:
Universalumas: Tinka plačiam metalų ir storių diapazonui.
Santykinis įrangos paprastumas: Pradinis barjeras dažnai yra žemesnis.
Lankstumas: Galimybė rankiniu būdu suvirinti sunkiai pasiekiamose vietose.
Mažos pradinės investicijos: Įranga paprastai yra pigesnė.
Trūkumai:
Didelė šilumos įvestis: Lemiasi didelės termiškai paveiktos zonos (TPZ), deformacijos ir liekamieji įtempiai.
Mažas greitis: Palyginti su lazeriniu suvirinimu, procesas gali būti žymiai lėtesnis.
Poreikis papildomoms medžiagoms: Dažnai reikalingos papildomos medžiagos siūlei formuoti.
Poapdorojimas: Dėl siūlės pločio ir nelygumų dažnai reikalingas šlifavimas ar kitas siūlės apdorojimas.
Poveikis operatoriui: Dujų, dūmų išsiskyrimas ir intensyvus UV spinduliavimas.
Lazerinis suvirinimas
Lazerinis suvirinimas naudoja fokusuotą, didelio energijos tankio lazerio spindulį medžiagoms lydyti ir sujungti. Ši technologija užtikrina labai tikslų ir koncentruotą šilumos įvedimą.
Privalumai:
Minimali šilumos įvestis ir maža TPZ: Sumažina deformacijas, liekamuosius įtempius ir leidžia suvirinti termiškai jautrias medžiagas.
Didelis suvirinimo greitis: Žymiai pralenkia tradicinius metodus, didinant našumą.
Didelis suvirinimo siūlės tikslumas ir kokybė: Siaura, gili ir lygi siūlė, kuriai dažnai nereikia poapdorojimo.
Galimybė suvirinti skirtingas medžiagas: Leidžia jungti skirtingus metalus ir lydinius.
Bekontaktis procesas: Mechaninio kontakto su ruošiniu nebuvimas sumažina įrankių nusidėvėjimą.
Automatizavimo potencialas: Idealiai tinka robotizuotoms sistemoms ir didelio tikslumo masinei gamybai.
Ekologiškumas: Mažiau dūmų ir dujų, palyginti su lankiniu suvirinimu.
Trūkumai:
Didelės pradinės investicijos: Lazerinio suvirinimo įranga yra žymiai brangesnė.
Sudėtingas nustatymas: Reikalingas aukštos kvalifikacijos personalas montavimui ir kalibravimui.
Griežti reikalavimai briaunų paruošimui: Reikalingas didelis detalių suderinimo tikslumas.
Medžiagos storio apribojimai: Labai storiems medžiagoms gali prireikti daugkartinio suvirinimo arba hibridinių metodų naudojimo.
Saugumo reikalavimai: Intensyvus lazerio spinduliavimas reikalauja griežtų saugos priemonių ir apsaugos.
Lyginamoji analizė
Lazerinio suvirinimo ateitis atrodo labai perspektyvi. Nuolat tobulėjant lazerinėms technologijoms (pvz., pluošto lazeriai tampa galingesni ir prieinamesni), jų taikymas tik plėsis.
Pagrindinės tendencijos ir perspektyvos:
Hibridinis suvirinimas: Lazerinio ir lankinio suvirinimo derinys (pvz., lazerinis-lankinis suvirinimas) sujungia abiejų metodų privalumus, užtikrinant didelį greitį ir gilų įsiskverbimą, išlaikant lankstumą.
Plonų medžiagų lazerinis suvirinimas ir mikro suvirinimas: Didėjantis tikslumas leidžia dirbti su itin plonomis medžiagomis ir mikroelektronikoje.
Adityvioji gamyba: Lazerinis suvirinimas yra pagrindinis komponentas kai kuriose metalo 3D spausdinimo technologijose, tokiose kaip tiesioginis lazerinis nusodinimas (DED).
Robotikos ir DI plėtra: Lazerinio suvirinimo integravimas su pažangiais robotais ir dirbtinio intelekto sistemomis leis sukurti visiškai autonomius ir adaptyvius suvirinimo kompleksus.
Energijos efektyvumas: Naujos kartos lazeriai tampa energijos efektyvesni, o tai sumažina eksploatavimo išlaidas.
Galingumo didinimas: Lazerio galios augimas leis suvirinti storesnes medžiagas, išlaikant didelį greitį ir kokybę.
Nors lazerinis suvirinimas reikalauja didesnių pradinių investicijų, jis siūlo didelius pranašumus tikslumo, greičio ir kokybės atžvilgiu, todėl yra pageidaujamas pasirinkimas aukštųjų technologijų gamybai. Ilgalaikėje perspektyvoje, mažėjant įrangos kainai ir toliau tobulėjant technologijoms, jis vaidins vis svarbesnį vaidmenį šiuolaikinėje pramonėje.
Išmaniosios gamyklos: Kaip pramonė 4.0 keičia gamybą
Išmaniosios gamyklos: Kaip pramonė 4.0 keičia gamybą?
Pramonė 4.0, arba Ketvirtoji pramonės revoliucija, reiškia esminius pokyčius gamybos aplinkoje, kuriuos apibūdina gilus skaitmeninių technologijų integravimas. Jos pagrindinis elementas yra „išmaniosios gamyklos“ (Smart Factories) – gamybos sistemos, kuriose mašinos, įranga, produktai ir žmonės sąveikauja realiuoju laiku, sukurdami savaime besiorganizuojančią ir savaime besireguliuojančią aplinką.
Kas yra pramonė 4.0 ir išmaniosios gamyklos?
Pramonė 4.0 – tai koncepcija, apibūdinanti gamybos procesų skaitmenizavimą ir automatizavimą naudojant pažangias technologijas. Tikslas yra sukurti tarpusavyje susijusias, intelektualias ekosistemas, kurios gali mokytis, prisitaikyti ir diegti naujoves.
Išmaniosios gamyklos – tai gamybos objektai, aprūpinti prijungtomis mašinomis, automatizuotomis sistemomis ir duomenimis valdomais procesais. Jos didina efektyvumą ir sumažina žmogiškąsias klaidas, kuriant lanksčias, savaime besiorganizuojančias sistemas.
Pagrindinės pramonės 4.0 technologijos
Gamybos transformacija pagal pramonę 4.0 remiasi keliomis pagrindinėmis technologijomis:
Daiktų internetas (IoT): Leidžia mašinoms, įrenginiams ir sistemoms keistis duomenimis realiuoju laiku, renkant informaciją apie įrangos būklę ir optimizuojant procesus.
Dirbtinis intelektas (DI) ir mašininis mokymasis: Naudojami didelių duomenų kiekių analizei, dėsningumų nustatymui, gedimų prognozavimui, procesų automatizavimui ir sprendimų priėmimui realiuoju laiku.
Didieji duomenys ir analizė: Didžiulių duomenų masyvų rinkimas ir analizė leidžia aptikti paslėptus dėsningumus, optimizuoti logistiką, sumažinti išlaidas ir pagerinti produkto kokybę.
Debesų kompiuterija: Suteikia keičiamo dydžio infrastruktūrą duomenų saugojimui ir apdorojimui, užtikrinant nepertraukiamą ryšį tarp mašinų, žmonių ir sistemų.
Pramoninė robotika ir automatizavimas: Robotai perima pasikartojančias ir pavojingas užduotis, didindami našumą, mažindami klaidų skaičių ir užtikrindami nepertraukiamą gamybą.
Kibernetinės-fizinės sistemos: Integruoja skaičiavimo ir fizinius komponentus, leidžiančias fiziniams procesams sąveikauti su skaitmeninėmis sistemomis.
Kaip pramonė 4.0 keičia gamybą?
Pramonės 4.0 įdiegimas lemia reikšmingus pokyčius gamybos sektoriuje:
Efektyvumo ir našumo didinimas: Užduočių automatizavimas, darbo procesų optimizavimas ir atliekų mažinimas žymiai padidina gamybą, sunaudojant mažiau išteklių.
Kokybės kontrolės gerinimas: DI ir duomenų analizės sistemos užtikrina nuolatinį kokybės stebėjimą ir kontrolę kiekviename gamybos etape, sumažindamos defektus ir pagerindamos produkto nuoseklumą.
Prevencinė priežiūra: Jutikliai ir analizė leidžia prognozuoti įrangos gedimus dar prieš jiems atsirandant, sumažinant prastovos laiką ir remonto išlaidas.
Sumažintos išlaidos: Procesų optimizavimas, efektyvus išteklių naudojimas, atliekų mažinimas ir prevencinė priežiūra prisideda prie veiklos sąnaudų mažinimo.
Padidėjęs lankstumas ir individualizavimas: Išmaniosios gamyklos gali greitai prisitaikyti prie paklausos pokyčių, gamindamos personalizuotus produktus dideliais kiekiais su minimaliomis papildomomis išlaidomis.
Pagerinta sauga ir darbo sąlygos: Pavojingų užduočių automatizavimas ir jutiklių naudojimas darbo aplinkai stebėti sumažina nelaimingų atsitikimų ir traumų riziką.
Tvarumas ir ekologiškumas: Pramonės 4.0 technologijos leidžia optimizuoti energijos suvartojimą, sumažinti išmetamųjų teršalų ir atliekų kiekį, prisidedant prie tvaresnės gamybos.
Ateities perspektyvos
Pramonė 4.0 toliau vystosi, ir jau atsiranda Pramonės 5.0 koncepcijos, kurios orientuojasi į glaudesnį bendradarbiavimą tarp žmonių ir mašinų. DI, tikėtina, vaidins dar svarbesnį vaidmenį šiame poslinkyje, užtikrindamas ne tik automatizavimą, bet ir intelektualią sąveiką, kurioje mašinos ir žmonės dirba kartu siekdami bendrų tikslų.
Robotizuotų sistemų naudojimas metalo konstrukcijų gamyboje: Ateitis jau čia
Robotizuotų sistemų naudojimas metalo konstrukcijų gamyboje: Ateitis jau čia
Metalo konstrukcijų gamyba, tradiciškai siejama su sunkiu fiziniu darbu ir sudėtingomis rankinėmis operacijomis, išgyvena tikrą revoliuciją dėl robotizuotų sistemų diegimo. Šios pažangios technologijos ne tik automatizuoja procesus; jos transformuoja visą pramonę, didindamos tikslumą, saugumą ir efektyvumą.
Kodėl robotai metalo apdirbime?
Šiuolaikiniame pasaulyje konkurencija verčia įmones ieškoti naujų gamybos optimizavimo būdų. Robotizacija metalo konstrukcijų gamyboje siūlo daugelio pagrindinių problemų sprendimą:
Tikslumo ir kokybės didinimas: Robotai atlieka pasikartojančias užduotis su neįtikėtinu tikslumu ir stabilumu, minimizuodami žmogiškąjį faktorių ir defektus. Tai ypač svarbu suvirinimui, pjovimui ir lenkimui, kur nukrypimai gali sukelti rimtų problemų.
Produktyvumo didinimas: Robotai gali dirbti visą parą, be pertraukų ir nuovargio, žymiai sutrumpindami gamybos ciklo laiką.
Darbo sąlygų ir saugumo gerinimas: Žmogaus pašalinimas iš pavojingų ir monotoniškų operacijų, tokių kaip suvirinimas nepatogiose padėtyse, darbas su sunkiais ruošiniais ar aukštoje temperatūroje, sumažina traumų ir profesinių ligų riziką.
Gamybos sąnaudų mažinimas: Nepaisant pradinių investicijų, robotizuotos sistemos atsiperka dėl broko sumažinimo, medžiagų taupymo, darbo jėgos poreikio sumažinimo ir bendro efektyvumo padidinimo.
Gamybos lankstumas: Šiuolaikiniai robotai lengvai perprogramuojami įvairioms užduotims atlikti ir dirbti su skirtingų tipų gaminiais, o tai leidžia greitai prisitaikyti prie kintančių rinkos reikalavimų.
Pagrindinės robotų taikymo sritys
Robotizuotos sistemos plačiai naudojamos įvairiuose metalo konstrukcijų gamybos etapuose:
Robotizuotas suvirinimas: Tai bene labiausiai paplitęs pritaikymas. Suvirinimo robotai užtikrina stabilią siūlės kokybę, didelį suvirinimo greitį ir galimybę dirbti su sunkiai pasiekiamomis vietomis. Jie gali atlikti tiek lankinį, tiek lazerinį suvirinimą, užtikrindami idealų sujungimą atsakingoms konstrukcijoms.
Robotizuotas pjovimas: Lazerinis, plazminis ar hidroabrazyvinis pjovimas naudojant robotus leidžia pasiekti didelį sudėtingos formos metalo pjovimo tikslumą, sumažinant atliekas ir tolesnio apdirbimo poreikį.
Lenkimas ir formavimas: Robotai integruojami su lakštų lenkimo presais ir kitomis formavimo mašinomis, automatizuodami ruošinių tiekimą ir pozicionavimą, o tai padidina lenkimo greitį ir tikslumą.
Paviršiaus apdirbimas: Robotai naudojami metalo konstrukcijų šlifavimui, poliravimui, siūlių valymui ir dažymui, užtikrinant tolygų padengimą ir aukštą paviršiaus kokybę.
Krovimo ir iškrovimo operacijos: Sunkieji pramoniniai robotai yra nepakeičiami dideliems ir sunkiems metalo ruošiniams perkelti, o tai padidina saugumą ir sumažina fizinį krūvį personalui.
Kokybės kontrolė: Robotai, aprūpinti mašininės regos sistemomis ir 3D skeneriais, gali automatiškai patikrinti geometrinius parametrus, defektų buvimą ir suvirintų siūlių kokybę, užtikrindami griežtą kontrolę kiekviename gamybos etape.
Iššūkiai ir perspektyvos
Robotizuotų sistemų diegimas nėra be iššūkių. Tai apima dideles pradines investicijas, personalo perkvalifikavimo (nuo operatorių iki inžinierių-programuotojų) poreikį, taip pat naujų sistemų integravimo su esama įranga sudėtingumą.
Tačiau robotizacijos atveriamos perspektyvos nusveria šiuos sunkumus. Vystantis dirbtiniam intelektui ir mašininiam mokymuisi, robotai tampa dar išmanesni, gebantys prisitaikyti ir mokytis. Plečiasi kolaboratyvių robotų (kobotų) taikymas, kurie gali saugiai dirbti greta žmogaus, atlikdami rutinines ar pavojingas užduotis.
Metalo konstrukcijų gamyba juda link visiškai automatizuotų ir išmanių gamyklų, kur robotai atliks pagrindinį vaidmenį, užtikrindami beprecedentį efektyvumo, tikslumo ir saugumo lygį. Įmonės, kurios pirmosios įsisavins šias technologijas, įgis didelį konkurencinį pranašumą rinkoje.
Adityviųjų technologijų (3D spausdinimo) taikymas metalo apdirbime: nauja gamybos era
Adityviųjų technologijų (3D spausdinimo) taikymas metalo apdirbime: nauja gamybos era
Adityviosios technologijos, arba 3D spausdinimas, kažkada atrodžiusios kaip mokslinė fantastika, šiandien transformuoja daugelį pramonės šakų, ir metalo apdirbimas nėra išimtis. Nuo prototipų kūrimo iki sudėtingų funkcinių detalių gamybos – metalo 3D spausdinimas atveria precedento neturinčias galimybes, papildydamas ir kai kuriais atvejais pakeisdamas tradicinius apdirbimo metodus.
Kas yra adityviosios technologijos metalo apdirbime?
Skirtingai nuo tradicinio (atimamojo) metalo apdirbimo, kai medžiaga pašalinama norimai formai gauti, adityviosios technologijos konstruoja objektus sluoksnis po sluoksnio, pridedant medžiagą. Metalams tai dažniausiai atliekama naudojant metalo miltelius ir galingus energijos šaltinius, tokius kaip lazeriai ar elektronų spinduliai, kurie sulydo miltelių daleles.
Pagrindiniai metalo 3D spausdinimo metodai:
Selektyvinis lazerinis sukepinimas/lydymas (SLS/SLM): Lazeris selektyviai lydo arba sukepina metalo miltelius sluoksnis po sluoksnio.
Tiesioginis lazerinis metalo nusodinimas (DED): Metalo milteliai tiekiami į sufokusuotą lazerio spindulį, kuris juos lydo, formuodamas sluoksnį po sluoksnio.
Rišiklio purškimas (Binder Jetting): Rišiklis užpurškiamas ant metalo miltelių sluoksnių, formuodamas dalį, kuri vėliau sukepinama krosnyje.
Medžiagos ekstruzija (Material Extrusion – Bound Metal Deposition): Panašu į FDM polimerų spausdinimą, tačiau naudojami metalo milteliai, sumaišyti su rišikliu, po to atliekamas sukepinimas.
3D spausdinimo privalumai metalo apdirbimui
Adityviųjų technologijų taikymas metalo apdirbime turi keletą reikšmingų privalumų:
Sudėtinga geometrija ir dizaino optimizavimas: Galimybė kurti detales su neįtikėtinai sudėtinga vidine struktūra, tokia kaip gardelės konstrukcijos, aušinimo kanalai ar tuščiavidurės formos. Tai leidžia optimizuoti detalės svorį, pagerinti jos funkcines charakteristikas (pvz., šilumos mainus) ir kurti individualizuotus gaminius.
Sutrumpintas prototipų kūrimo laikas ir sumažintos sąnaudos: Greitas funkcinių prototipų gamyba tiesiogiai iš 3D modelio žymiai pagreitina produkto kūrimo ciklus ir sumažina įrankių sąnaudas.
Medžiagų atliekų minimizavimas: Priešingai nei atimamieji metodai, kai didžioji dalis medžiagos gali pavirsti drožlėmis, adityviniai procesai generuoja žymiai mažiau atliekų, o tai ypač naudinga dirbant su brangiais ir retais metalais.
Gamyba pagal užsakymą ir individualizavimas: Galimybė gaminti unikalias ar mažų partijų detales be brangaus įrangos perkonfigūravimo. Tai idealiai tinka specializuotiems įrankiams, medicininiams implantams ar atsarginėms dalims pasenusiai įrangai kurti.
Detalių remontas ir atnaujinimas: Kai kurie adityviniai procesai, pavyzdžiui, DED, gali būti naudojami medžiagai pridėti prie pažeistų metalinių detalių, atstatant jų funkcionalumą ir prailginant tarnavimo laiką.
Taikymo sritys
Adityviosios technologijos jau aktyviai naudojamos įvairiuose metalo apdirbimo sektoriuose:
Aviacijos ir kosmoso pramonė: Lengvų, tvirtų ir sudėtingų orlaivių ir erdvėlaivių komponentų (pvz., turbinų menčių, laikiklių) gamyba.
Medicina: Individualių implantų (pvz., sąnarių protezų, kaukolės plokštelių), chirurginių instrumentų ir dantų konstrukcijų kūrimas.
Automobilių pramonė: Prototipų, funkcinių sportinių automobilių dalių, taip pat įrankių ir armatūros gamyba.
Energetika: Dujų turbinų, šilumokaičių ir kitų ekstremaliomis sąlygomis veikiančių elementų komponentų gamyba.
Įrankių gamyba: Liejimo formų su integruotais aušinimo kanalais, skirtų liejimui slėgiu, kūrimas, kas sutrumpina ciklo laiką ir pagerina produkto kokybę.
Iššūkiai ir ateitis
Nepaisant visų privalumų, adityviosios technologijos metalo apdirbime susiduria su keletu iššūkių:
Didelės įrangos ir medžiagų sąnaudos: Investicijos į pramoninius metalo 3D spausdintuvus ir specializuotus miltelius išlieka reikšmingos.
Gamybos greitis: Didelės apimties serijinei gamybai adityviniai procesai vis dar gali būti lėtesni, palyginti su tradiciniais metodais.
Paviršiaus kokybė ir po apdirbimo: 3D spausdintos detalės dažnai reikalauja papildomo mechaninio apdirbimo, kad būtų pasiektas norimas paviršiaus lygumas ir tikslumas.
Standartizavimas ir kvalifikacija: Pramonės standartų kūrimas ir personalo kvalifikacija darbui su šiomis sudėtingomis technologijomis vis dar vyksta.
Tačiau nuolatiniai tyrimai ir plėtra, mažėjančios įrangos ir medžiagų sąnaudos, taip pat naujų, greitesnių ir tikslesnių spausdinimo metodų atsiradimas rodo, kad adityviosios technologijos vaidins vis svarbesnį vaidmenį metalo apdirbimo ateityje, atveriančios duris inovacijoms ir gamybos transformacijai.
CNC staklių vystymosi tendencijos didelio tikslumo metalo apdirbimui
CNC staklių vystymosi tendencijos didelio tikslumo metalo apdirbimui
Pasaulyje, kuriame tikslumas ir efektyvumas yra pagrindiniai sėkmės veiksniai, kompiuterinio skaitmeninio valdymo (CNC) staklės ir toliau išlieka didelio tikslumo metalo apdirbimo širdimi. Šios mašinos nuolat tobulėja, prisitaikydamos prie naujų pramonės poreikių ir siūlydamos neprilygstamas galimybes kurti sudėtingas ir aukštos kokybės detales. Apžvelkime pagrindines tendencijas, kurios formuoja šios gyvybiškai svarbios pramonės ateitį.
1. Išmanioji automatizacija ir integracija su robotika
Šiuolaikinės CNC staklės neapsiriboja tik programų vykdymu. Jos tampa integruotų automatizuotų sistemų dalimi. Robotai vis dažniau naudojami automatiniam ruošinių pakrovimui ir iškrovimui, įrankių keitimui ir netgi po apdirbimo, sumažinant žmogaus įsikišimą ir didinant produktyvumą. Tai ypač svarbu serijinei gamybai, kur svarbiausia yra pakartojamumas ir greitis.
2. Išplėstinės daugiakryptės apdirbimo galimybės
Staklės su 5, 7 ir daugiau ašių nebėra retenybė, o tampa standartu didelio tikslumo metalo apdirbimui. Šios mašinos leidžia apdoroti sudėtingos geometrijos detales vienu nustatymu, sumažinant gamybos laiką, pašalinant klaidas, susijusias su perkrovimu, ir žymiai pagerinant tikslumą. Galimybė apdirbti įvairiais kampais atveria duris novatoriškoms formoms, kurios anksčiau buvo nepasiekiamos.
3. Pramonės 4.0 ir daiktų interneto (IIoT) integravimas
CNC staklių prijungimas prie bendro gamybos tinklo per IIoT yra ne tik tendencija, bet ir būtinybė. Tai leidžia realiuoju laiku stebėti įrangos veikimą, rinkti duomenis apie produktyvumą, prognozuoti gedimus ir atlikti numatytąją priežiūrą. Toks požiūris žymiai padidina efektyvumą, sumažina prastovų laiką ir optimizuoja resursų naudojimą. Staklių skaitmeniniai dvyniai leidžia modeliuoti procesus ir optimizuoti programas prieš pradedant realų apdirbimą.
4. Hibridinės technologijos: atimamosios ir adityviosios gamybos simbiozė
Viena iš įdomiausių tendencijų yra hibridinių staklių atsiradimas, kurios sujungia tradicinį atimamąjį (medžiagos pašalinimas) ir adityvųjį (medžiagos sluoksniavimas, 3D spausdinimas) apdirbimą. Tai atveria naujus horizontus kuriant detales su sudėtinga vidine struktūra, mažinant atliekas ir taisant pažeistas brangias dalis. Pavyzdžiui, galima atspausdinti detalės pagrindą, o po to tiksliai apdirbti jos paviršius.
5. Padidėjęs energijos efektyvumas ir ekologiškumas
Augant dėmesiui tvariai plėtrai, CNC staklių gamintojai aktyviai siekia sumažinti savo mašinų energijos sąnaudas. Efektyvesnių variklių, aušinimo sistemų ir programinės įrangos, optimizuojančios įrankio trajektorijas, naudojimas padeda sumažinti anglies pėdsaką ir eksploatavimo išlaidas. Taip pat pastebimas perėjimas prie ekologiškesnių pjovimo skysčių ir atliekų šalinimo sistemų.
6. Dirbtinis intelektas (DI) ir mašininis mokymasis valdyme
DI ir mašininis mokymasis pradeda vaidinti svarbų vaidmenį optimizuojant apdirbimo procesus. Šios technologijos naudojamos automatiniam pjovimo sąlygų pritaikymui prie besikeičiančių aplinkybių, įrankio nusidėvėjimo prognozavimui, anomalijų aptikimui ir netgi optimalių įrankio trajektorijų generavimui. Tai užtikrina stabilesnį veikimą, pagerina paviršiaus kokybę ir prailgina įrankio tarnavimo laiką.
Išvada
CNC staklių vystymosi tendencijos didelio tikslumo metalo apdirbimui rodo ateitį, kurioje mašinos bus dar išmanesnės, autonomiškesnės ir universalesnės. Įmonėms, siekiančioms išlikti konkurencingomis, itin svarbu sekti šias inovacijas ir integruoti jas į savo gamybos procesus. Investicijos į pažangias CNC technologijas yra investicijos į tikslumą, produktyvumą ir tvarią plėtrą.
Didelės entropijos lydinių detalių apdirbimas: iššūkiai ir galimybės
Didelės entropijos lydinių detalių apdirbimas: iššūkiai ir galimybės
Įvadas
Didelės entropijos lydiniai (DEL) – tai naujos kartos metalai, sudaryti iš penkių ar daugiau pagrindinių elementų panašiu santykiu. Jie išsiskiria dideliu kietumu, stiprumu, atsparumu karščiui ir korozijai, todėl plačiai tiriami aviacijos, energetikos ir gynybos srityse.
Tačiau DEL apdirbimas yra sudėtingas – jų struktūra sukelia padidėjusį įrankių dilimą ir reikalauja nestandartinių technologinių sprendimų.
Pagrindiniai iššūkiai
1. Didelis kietumas ir stiprumas
DEL dažnai viršija 400–500 HV kietumą bei 1000 MPa tempimo stiprumą, todėl apdirbant reikia daugiau jėgos, o įrankiai greičiau dėvisi.
2. Mažas šilumos laidumas
Šiluma susikaupia pjovimo zonoje, perkaitindama detalę ir įrankį. Būtinas efektyvus aušinimas.
3. Anizotropija ir struktūros nevienalytiškumas
DEL gali turėti kintančias minkštas ir kietas sritis, kas sukelia vibracijas ir blogina paviršiaus kokybę.
Apdirbimo galimybės
Įrankių parinkimas
-
Karbido frezos su nano danga (TiAlN, AlCrN)
-
Keraminiai ir CBN įdėklai baigiamajam tekinimui
-
DLC ir deimanto tipo dangos minkštesniems lydiniams
Optimali pjovimo strategija
-
Mažesnis pjovimo greitis ir padavimas (20–40 % mažesni)
-
Nedidelis pjūvio gylis, bet stabili trajektorija
Aušinimas
-
Aukšto slėgio aušinimo sistemos (HPC), MQL
-
Kai kada – sausas pjovimas su optimizuota geometrija
Palyginimas su kitais metalais
Medžiaga | Apdirbamumas | Pastabos |
---|---|---|
Didelio stiprumo titanas | ★★☆☆☆ | Mažas šilumos laidumas, didelis dilimas |
Nerūdijantis plienas 316 | ★★★☆☆ | Geras su aušinimu |
Inconel (Ni lydinys) | ★☆☆☆☆ | Labai greitas įrankių dėvėjimasis |
DEL (pvz. CoCrFeMnNi) | ★★☆☆☆ | Sudėtingas, bet įveikiamas su korekcijomis |
Ateities kryptys
Kad DEL taptų plačiai naudojami, būtina:
-
Kurti naujus įrankių medžiagų sprendimus
-
Naudoti pažangų proceso monitoringą
-
Integruoti hibridines apdirbimo technologijas (pvz., EDM + frezavimą)
Išvados
Didelės entropijos lydinių apdirbimas reikalauja žinių ir pasiruošimo, tačiau tai – pažangių pramonės šakų ateitis. Su tinkamomis technologijomis ir inovacijomis jų apdirbimas tampa vis efektyvesnis.
Nanodangos pjovimo įrankiams: ilgaamžiškumas ir atsparumas dėvėjimuisi
Nanodangos pjovimo įrankiams: ilgaamžiškumas ir atsparumas dėvėjimuisi
Įvadas
-
Šiuolaikinis metalo apdirbimas reikalauja tikslumo ir įrankio stabilumo
-
Briaunos dėvėjimasis lemia broką ir prastovas
-
Sprendimas: nanodangos, kurios kelis kartus prailgina įrankių tarnavimą
Kas yra nanodangos?
-
Itin ploni (dešimtys nanometrų) daugiasluoksniai sluoksniai
-
Gaminami iš nitridų, karbidų, oksidų (naudojant PVD/CVD)
-
2–7 sluoksniai, kiekvienas mažiau nei 100 nm
Nanodangų privalumai
-
Atsparumas dėvėjimuisi
-
Mažesnė trintis
-
Atsparumas šilumai ir chemijai
-
Įrankio tarnavimo laikas x2–x5
Nanodangų rūšys
Danga | Sudėtis | Savybės |
---|---|---|
TiAlN | Titano-aliuminio nitridas | Karščiui atspari, universali |
AlTiN | Daugiau Al nei Ti | Tinka dideliam pjovimo greičiui |
CrN | Chromo nitridas | Atspari korozijai |
DLC | Deimantinė anglis | Labai maža trintis, puikiai tinka spalviesiems metalams |
nACo® | TiAlN/Si₃N₄ nanokompozitas | Maksimalus atsparumas dėvėjimuisi |
Užnešimo technologijos
-
PVD — mažai šilumos, ekologiška
-
CVD — gilesnis įsiskverbimas, tinka dideliems įrankiams
-
Naujos: HiPIMS, ALD, nano laminatai
Pavyzdžiai
-
TiAlN: +300% tarnavimo trukmė nerūdijančiam plienui
-
DLC: minimalus dilimas aliuminiui ir variui
-
Inconel-718: didesnė eiga, mažiau vibracijų
Tinkamos dangos pasirinkimas
Apdirbamas metalas | Rekomenduojama danga |
---|---|
Anglinis plienas | TiAlN, AlTiN |
Titano lydiniai | nACo, AlTiN |
Aliuminis, varis | DLC, CrN |
Karščiui atsparūs lydiniai | nACo, daugiasluoksnė AlTiN |
Ateitis
-
Savęs atstatantys sluoksniai
-
„Protingos“ dangos, reaguojančios į apkrovą
-
Kombinuotos (PVD + ALD)
-
Nano-trinties valdymo technologijos
Išvada
-
Nanodangos sumažina įrankių sąnaudas ir pagerina apdirbimo patikimumą
-
Teisingas dangos pasirinkimas = geresni rezultatai
-
Ateitis priklauso pažangioms, tvarioms nano-inžinerinėms dangoms
Ekologiški pjovimo skysčiai: augalinės kilmės aliejų alternatyvos
Ekologiški pjovimo skysčiai: augalinės kilmės aliejų alternatyvos
Įvadas
-
Pjovimo skysčiai būtini metalo apdirbime
-
Tradiciniai skysčiai – toksiški, sunkiai utilizuojami
-
Auga poreikis tvariems sprendimams gamyboje
Kodėl augalinės kilmės?
-
Pagaminti iš sojų, rapsų, saulėgrąžų, palmių
-
Biologiškai skaidomi, nekenksmingi
-
Mažina utilizacijos kaštus, gerina darbo saugą
Augalinių pjovimo skysčių rūšys
-
Gryni augaliniai aliejai
-
Paprasti, bet greitai genda, oksiduojasi
-
-
Emulguojami bio-skysčiai
-
Maišomi su vandeniu, tinka įvairiems procesams
-
-
Sintetiniai riebalų rūgščių esteriai
-
Ilgiau tarnauja, atsparesni temperatūrai
-
Palyginimas
Parametras | Mineraliniai skysčiai | Augaliniai bio-skysčiai |
---|---|---|
Aplinkos poveikis | Didelis | Mažas |
Kaina | Mažesnė | Didesnė (atsiperka) |
Įrankių tarnavimo laikas | Vidutinis | Dažnai ilgesnis |
Utilizacija | Reikia apdorojimo | Biologiškai skaidomi |
Įgyvendinimo iššūkiai
-
Pradinės investicijos
-
Įrangos suderinamumas
-
Laikymo sąlygų jautrumas
Pavyzdžiai
-
Audi, Bosch naudoja rapsų pagrindu pagamintus skysčius
-
DMG Mori siūlo įrangą su bio-SOŽ palaikymu
-
Mažos dirbtuvės Skandinavijoje pereina prie bio-alternatyvų
Tendencijos
-
Universalūs bio-skysčiai
-
pH ir mikrobų stebėjimo sistemos
-
Uždari perdirbimo ciklai
Išvada
-
Augaliniai pjovimo skysčiai – aplinkai ir ekonomikai naudingi
-
Tinkamai įdiegus, tampa optimalia alternatyva
10 geriausių ultragarso ir precizinio CNC apdirbimo staklių
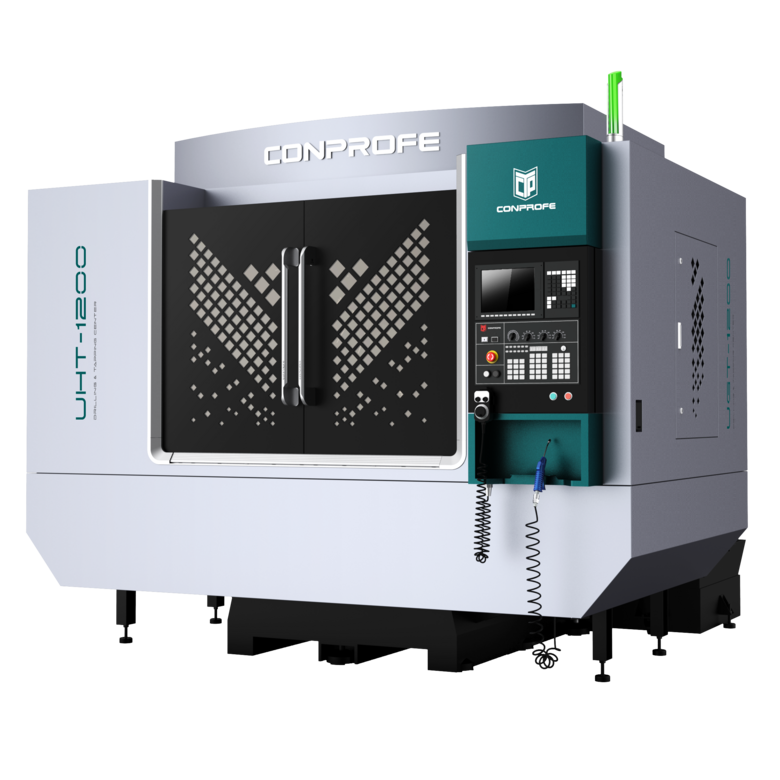
10 geriausių ultragarso ir precizinio CNC apdirbimo staklių
1. DAMA.ch ultragarso mikroapdirbimo sistemos
Šveicarija
Ekspertai ultraprecizinėje ultragarso apdirbimo srityje. Naudojamos optikai, MEMS, keramikai ir stiklui – užtikrina nanometrinį paviršiaus lygumą ir submikroninį tikslumą.
2. Conprofe ultragarso CNC centrai (ULM serija)
Kinija
3 ir 5 ašių CNC staklės su 16–60 kHz ultragarso vibracija. Skirtos apdirbti safyrą, keramiką, stiklą ir anglies pluoštą. Ekologiškos ir efektyvios sistemos.
3. DMG MORI Ultrasonic / LASERTEC serija
Vokietija / Japonija
Aukštos klasės 5 ašių ultragarso apdirbimo centrai su automatizacijos galimybėmis. Pritaikyti medicinos, optikos ir aviacijos sektoriams.
4. Yamazaki Mazak (Variaxis & Integrex)
Japonija
Tikslūs ir daugiafunkciniai CNC centrai su terminiu stabilumu.
5. Makino PS / T serija
Japonija
Didelio greičio ir tikslumo apdirbimo centrai liejimo formoms ir aviacijai. Siūlo terminį valdymą ir aukštą pakartojamumą.
6. GF Machining Solutions (Mikron, AgieCharmilles)
Šveicarija
Mikroapdirbimo ir EDM technologijų lyderiai, naudojami medicinoje ir laikrodžių pramonėje.
7. Okuma MB & Multus
Japonija
Patikimos ir tvirtos CNC staklės su termine kompensacija – puikiai tinka sudėtingoms detalėms.
8. FANUC Robodrill + automatizavimas
Japonija
Kompaktiški CNC centrai, suderinami su ultragarso įrankiais ir robotizacija.
9. Starrag (NB / LX / STC)
Šveicarija
5 ašių staklės turbinų ir aviacijos komponentų apdirbimui – ypač tikslios.
10. Mandelli Sistemi SPARK
Italija
Galingos horizontalios staklės automobilių ir aviacijos gamybai.
Kaip automatizuoti ruošinių pakrovimą: sprendimai mažoms dirbtuvėms
Kaip automatizuoti ruošinių pakrovimą: sprendimai mažoms dirbtuvėms
Mažose ir vidutinėse gamybinėse įmonėse automatizacija dažnai laikoma brangia ar neprieinama. Tačiau viena daugiausiai rankinio darbo reikalaujanti užduotis — ruošinių pakrovimas ir iškrovimas — jau šiandien gali būti automatizuota be milžiniškų išlaidų. Šiuolaikiniai sprendimai padeda padidinti našumą ir sumažinti įrangos nusidėvėjimą, net turint ribotą biudžetą ar erdvę.
Kodėl verta automatizuoti ruošinių pakrovimą
Problemos su rankiniu darbu:
-
Žmogiškos klaidos ir nuovargis
-
Pertraukos, nelygus tempas
-
Ribotas darbo ciklo greitis
-
Nestabili kokybė dėl netikslaus padėjimo
Automatizavimo privalumai:
-
Stabilus darbo ritmas
-
Mažiau klaidų ir broko
-
Galimybė dirbti be operatoriaus
-
Geresnis įrangos atsiperkamumas
-
Mažesnės darbo sąnaudos
Sprendimų variantai mažoms įmonėms
1. Gravitaciniai ir vibraciniai padavėjai
Tinka mažoms detalėms (varžtams, poveržlėms).
-
Paprasta konstrukcija
-
Tinka serijinei gamybai
-
Kaina: €500–€2,000
2. Pneumatinės padavimo sistemos
-
Tinka vidutinio dydžio ruošiniams
-
Mažos energijos sąnaudos
-
Galima pritaikyti senesnėse staklėse
3. Manipuliatoriai ir kolaboratyvūs robotai (cobotai)
-
Gali krauti, išimti, rūšiuoti ruošinius
-
Saugūs naudoti šalia žmonių
-
Pradinė kaina nuo €12,000
-
Tinka vienetinėms ir mažoms serijoms
4. Linijinės portalinės sistemos
-
Kompaktiškos, virš staklių
-
Efektyvios pasikartojančiuose procesuose
-
Užima mažai vietos
-
Lankstūs pritaikyme
5. Automatinės karuselės ir palečių keitimo stalai
-
Ruošiniai kraunami iš anksto
-
Sistema automatiškai paduoda
-
Leidžia dirbti be operatoriaus
Kaip išsirinkti tinkamą sprendimą
Klausimas | Į ką atkreipti dėmesį |
---|---|
Ruošinio tipas ir dydis | Svoris, forma, matmenys |
Gamybos apimtis | Vienetinė, maža ar vidutinė serija |
Turima erdvė | Įrenginių išdėstymas, prieinamumas |
Biudžetas | Ar įmanoma diegti etapais? |
Gamybos lankstumas | Ar dažnai keičiami gaminiai? |
Diegimo etapai
-
Išanalizuokite dabartinius procesus
-
Pasirinkite pilotinę vietą
-
Parinkite technologiškai tinkamą sprendimą
-
Užtikrinkite saugumą
-
Apmokykite darbuotojus
-
Įvertinkite rezultatus po diegimo
Praktinis pavyzdys
Frėzavimo cechas su trimis CNC staklėmis ir dviem operatoriais prarado daug laiko rankiniam pakrovimui.
Sprendimas:
Įdiegtas pigus robotas su dvigubu griebtuvu.
Rezultatas:
-
Gamybos apimtis padidėjo 28 %
-
Brokas sumažėjo 14 %
-
Investicija atsipirko per 9 mėnesius
Išvada
Ruošinių pakrovimo automatizavimas — tai protingas žingsnis net ir mažiems gamintojams. Šiandienos sprendimai yra prieinami, kompaktiški ir lengvai įdiegami, padedant pereiti prie išmanesnės ir konkurencingesnės gamybos.
IIoT integracija metalo apdirbime: privalumai ir pirmie žingsniai
IIoT integracija metalo apdirbime: privalumai ir pirmie žingsniai
Skaitmeninės transformacijos laikais vis daugiau gamybos įmonių renkasi IIoT (Industrial Internet of Things – Pramoninis daiktų internetas) technologijas. Metalo apdirbimo srityje tai ypač aktualu dėl didelio efektyvumo ir tikslumo reikalavimų.
Kas yra IIoT ir kodėl verta jį taikyti metalo apdirbime?
IIoT apima jutiklius, įrenginius ir programinę įrangą, kurie renka ir perduoda duomenis realiu laiku. Tai leidžia:
-
nuolat stebėti įrangą,
-
laiku pastebėti gedimus,
-
optimizuoti gamybos ciklą,
-
atlikti duomenų analizę.
Pavyzdys:
CNC staklės siunčia informaciją apie temperatūrą, vibracijas, apkrovą ir ciklų laiką. Sistema įspėja techniką apie galimus gedimus dar prieš jiems įvykstant.
Pagrindiniai privalumai
-
Mažesnės prastovos
-
Didesnis produktyvumas
-
Resursų taupymas
-
Skaidrumas ir kontrolė
-
Aukštesnė kokybė
Pirmieji žingsniai
-
Įvertinkite esamą įrangą ir poreikius
-
Nustatykite prioritetinius duomenis
-
Įdiekite jutiklius, pradėkite rinkti duomenis
-
Pasirinkite platformą (pvz., Siemens MindSphere)
-
Apmokykite darbuotojus
-
Įgyvendinkite pilotinį projektą
Ką galima automatizuoti jau dabar
-
CNC įrangos stebėjimą
-
Vibracijos ir perkaitimo įspėjimus
-
Prastovų sekimą
-
Įrankių nusidėvėjimo stebėjimą
-
Kokybės kontrolę realiu laiku
Išvada
IIoT yra ne ateitis, o dabartis. Pradėkite nuo vienos staklės ir auginkite skaitmeninę gamybą palaipsniui.
Kaip tinkamai prižiūrėti ir sukalibruoti lazerines sistemas, kad būtų užtikrintas pjovimo tikslumas
Kaip tinkamai prižiūrėti ir sukalibruoti lazerines sistemas, kad būtų užtikrintas pjovimo tikslumas
Įžanga
Lazerinio pjovimo įranga gali pasiekti aukštą tikslumą tik tada, kai ji reguliariai prižiūrima ir sukalibruojama. Dulkės, šiluma ir netikslūs optiniai nustatymai mažina veikimo efektyvumą.
1. Kodėl svarbi priežiūra
Prasta priežiūra sukelia:
-
Netikslius pjūvius ir atliekas;
-
Greitesnį komponentų susidėvėjimą;
-
Gaisro ar perkaitimo riziką;
-
Ilgesnį remontą ir didesnes išlaidas.
2. Kasdieninė priežiūra
-
Valykite lęšius ir veidrodžius su izopropilo alkoholiu ir mikropluošto šluoste.
-
Patikrinkite fokusavimą – rankiniu būdu ar automatine funkcija.
-
Patikrinkite aušinimo sistemą – skysčio lygis, nutekėjimai.
-
Išvalykite dulkes nuo pjovimo zonos ir ventiliacijos angų.
3. Savaitinė ir mėnesinė priežiūra
Kiekvieną savaitę:
-
Patikrinkite tvirtinimus ir veidrodžių padėtį.
-
Valykite ventiliatorius ir filtrus.
-
Įsitikinkite, kad diržai ir ašys juda sklandžiai.
Kiekvieną mėnesį:
-
Kalibruokite X ir Y ašis.
-
Pakeiskite optinius elementus, jei reikia.
-
Išbandykite lazerio spindulio padėtį.
4. Kalibravimo žingsniai
-
Optinės trajektorijos testas: paleiskite impulsus kampuose.
-
Fokusavimo bandymai: pjaukite linijas įvairiais aukščiais.
-
Ašių kalibracija: pjaukite tinklelį ir patikrinkite geometriją.
-
Programinės įrangos kalibravimas: reguliuokite žingsnius, kompensacijas.
5. Dažnos klaidos
Klaida | Pasekmė |
---|---|
Valymas pirštais/popieriumi | Subraižymas, šilumos iškraipymas |
Dėmesio trūkumas aušinimui | Perkaitimas, gedimai |
Nekalibruojama po judėjimo | Geometrinės klaidos |
6. Saugos patarimai
-
Prieš priežiūrą išjunkite maitinimą.
-
Naudokite pirštines ir lazerines apsaugines akinius.
-
Lęšius laikykite sausoje, dulkėms atsparioje vietoje.
Kaip pasirinkti tinkamiausią CNC įrangos aušinimo sistemą
Kaip pasirinkti tinkamiausią CNC įrangos aušinimo sistemą
Temperatūros kontrolė CNC apdirbime yra labai svarbi. Perkaitimas lemia įrankių dėvėjimąsi, detalių netikslumus ir apdorojimo nestabilumą. Tinkama aušinimo sistema padeda išlaikyti kokybę, ilgaamžiškumą ir našumą.
Straipsnyje apžvelgsime populiariausius aušinimo metodus, jų privalumus, trūkumus ir taikymo sritis.
Kodėl reikia aušinimo?
Pjovimo metu šiluma sukelia:
-
Įrankių susidėvėjimą
-
Dydžio netikslumus
-
Paviršiaus šiurkštumą
-
Detalės deformacijas
Efektyvus aušinimas mažina trintį, šalina šilumą ir pagerina drožlių šalinimą.
Pagrindiniai aušinimo būdai
1. Skystas aušinimas (emulsija, alyva)
Populiariausias metodas — skystis purškiamas į pjovimo zoną.
Privalumai:
-
Efektyvus šilumos pašalinimas
-
Pagerina drožlių šalinimą
-
Mažina įrankių susidėvėjimą
Trūkumai:
-
Reikia filtravimo ir priežiūros
-
Galima korozija
-
Didesnis poveikis aplinkai
Tinka:
Plienas, titanas, nikelio lydiniai, intensyvus pjovimas.
2. Minimalus tepimas (MQL)
Mažas kiekis alyvos purškiamas aerozolio pavidalu.
Privalumai:
-
Mažos sąnaudos
-
Švari darbo zona
-
Draugiška aplinkai
Trūkumai:
-
Mažesnis aušinimas nei skysčiu
-
Reikalingas tikslus purkštuko nustatymas
Tinka:
Aliuminis, plastikas, minkšti lydiniai.
3. Oro aušinimas
Suslėgtas oras pučiamas į pjovimo zoną.
Privalumai:
-
Paprasta sistema
-
Nereikia skysčių
-
Mažai priežiūros
Trūkumai:
-
Prastas aušinimo efektyvumas
-
Netinka kietoms medžiagoms
Tinka:
Plastikai, grafitas, minkšti metalai.
4. Kriogeninis aušinimas (skystas azotas, CO₂)
Naudojamos labai žemos temperatūros.
Privalumai:
-
Maksimaliai pailgina įrankių tarnavimo laiką
-
Aukšta paviršiaus kokybė
-
Neteršia aplinkos
Trūkumai:
-
Didelė kaina
-
Reikia specialios įrangos
Tinka:
Nikelio lydiniai, aviacija, medicina.
Kaip pasirinkti?
Medžiaga:
-
Kieti metalai → skystas ar kriogeninis
-
Aliuminis → MQL
-
Plastikas → oras
Apdirbimo intensyvumas:
-
Didesnis → efektyvesnis aušinimas
-
Mažesnis → pakanka sauso
Aplinkos sąlygos ir ekonomika:
-
Ar reikalingas švarus procesas?
-
MQL pigesnis, kriogeninis — brangesnis
Išvada
Nėra vieno sprendimo visiems atvejams. Pasirinkimas priklauso nuo jūsų poreikių. UDBU padeda rasti geriausią aušinimo sprendimą CNC apdirbimui.
Susisiekite su mumis, kad padidintumėte gamybos efektyvumą.
Naujų medžiagų apžvalga CNC apdirbimui: nuo kompozitų iki stiprių lydinių
Naujų medžiagų apžvalga CNC apdirbimui: nuo kompozitų iki stiprių lydinių
Šiuolaikinė gamyba vis dažniau susiduria su medžiagomis, kurios pasižymi mažu svoriu, dideliu atsparumu ir ilgaamžiškumu. Tokios medžiagos kaip kompozitai, titanas, nikelių lydiniai bei inžineriniai plastikai atveria naujas galimybes, tačiau reikalauja specifinių apdirbimo sprendimų.
Šioje apžvalgoje aptarsime pagrindinius medžiagų tipus, jų savybes ir praktinius patarimus CNC apdirbimui.
Anglies pluoštas (karbonas)
Privalumai:
-
Itin lengvas ir tvirtas
-
Atsparus korozijai
-
Gerai slopina vibracijas
Iššūkiai:
-
Greitas įrankių susidėvėjimas
-
Laminato sluoksniavimasis
-
Jautrumas vibracijoms
Rekomendacijos:
-
Naudoti deimantinį PCD įrankį
-
Įdiegti dulkių šalinimo sistemą
-
Sumažinti pjovimo jėgas ir vibracijas
Titano lydinys (pvz., Ti-6Al-4V)
Privalumai:
-
Didelis stiprumas ir atsparumas
-
Lengvas, bet tvirtas kaip plienas
-
Biologiškai suderinamas — tinka medicinai
Iššūkiai:
-
Silpna šilumos sklaida
-
Lipni drožlė
-
Brangi žaliava
Rekomendacijos:
-
Naudoti karbido įrankius su TiAlN ar AlCrN danga
-
Naudoti aukšto slėgio aušinimą
-
Dirbti su maža pastūma, vidutiniu greičiu
Nikelio superlydiniai (Inconel, Hastelloy, Waspaloy)
Privalumai:
-
Atsparūs ekstremalioms temperatūroms
-
Puikios antikorozinės savybės
-
Geometrinis stabilumas
Iššūkiai:
-
Didelės pjovimo jėgos
-
Greitas įrankių nusidėvėjimas
-
Kietėjimas pjovimo vietoje
Rekomendacijos:
-
Naudoti atsparius karbido įrankius
-
Stebėti įrankio nusidėvėjimą
-
Apdirbti mažomis pastūmomis
Stiprūs aliuminio lydiniai (7xxx serija)
Privalumai:
-
Lengvi ir tvirti
-
Atsparūs korozijai
-
Plačiai naudojami aviacijoje ir autosporte
Iššūkiai:
-
Drožlių sankaupos
-
Užsigrūdimai, užvyniojimai
Rekomendacijos:
-
Naudoti poliruotus pjovimo įrankius
-
Didelis greitis, mažas pastūmos spaudimas
-
Sausas arba MQL aušinimas
Inžineriniai plastikai (PEEK, PTFE, Delrin)
Privalumai:
-
Lengvi, atsparūs chemikalams
-
Elektros izoliacija
-
Lanksti apdirbimo galimybė
Iššūkiai:
-
Šiluminė deformacija
-
Ilgos, lipnios drožlės
-
Žemas standumas
Rekomendacijos:
-
Vienašmeniai aštrūs įrankiai
-
Aukšti apsisukimai, maža pastūma
-
Saugoti nuo perkaitimo
Išvada
Naujos medžiagos keičia gamybos standartus. Su tinkama įranga ir žiniomis jas galima apdirbti efektyviai. UDBU padės parinkti tinkamus sprendimus ir optimizuoti gamybą.
Susisiekite su mumis, jei norite dirbti efektyviau.
Detalių pakrovimo ir iškrovimo automatizavimas: kaip padidinti gamybos efektyvumą
Detalių pakrovimo ir iškrovimo automatizavimas: kaip padidinti gamybos efektyvumą
Šiuolaikinė gamyba reikalauja greičio, tikslumo ir nuoseklumo. CNC staklėse detalų pakrovimo/iškrovimo automatizavimas — tai raktas į našumą ir konkurencingumą.
Kodėl verta automatizuoti?
Rankinis darbas turi trūkumų:
-
Žmogaus klaidos dėl nuovargio
-
Staklių prastovos pakrovimo metu
-
Didėja nelaimingų atsitikimų rizika
Automatizacija šias problemas išsprendžia.
Kokios sistemos naudojamos?
1. Robotiniai manipuliatoriai
-
6 ašių pramoniniai robotai — sudėtingiems uždaviniams
-
Portaliniai robotai — didelėms ar sunkioms detalėms
-
Bendradarbiaujantys robotai (cobotai) — saugūs, paprasti valdyti, puikiai tinka mažoms įmonėms
2. Konvejeriai
-
Ritininiai — didelėms ir plokščioms detalėms
-
Juostiniai — universaliai paskirčiai
-
Moduliniai su rūšiavimu — detalių įvairovei
Integracija su CNC staklėmis
Reikia:
-
Duomenų mainų protokolų (OPC UA, Ethernet/IP)
-
Suderinamų CNC valdiklių
-
Saugumo įrangos: apsauginių barjerų, gaubtų, avarinių mygtukų
Valdymas vykdomas per PLC arba CNC programą.
Automatizacijos pranašumai:
-
Mažesnės darbo sąnaudos
-
Didėja našumas (iki 50%)
-
Stabili kokybė
-
Galimybė dirbti be žmogaus 24/7
-
Saugesnė darbo aplinka
Pavyzdžiai iš gamybos:
-
Aliuminio detalių gamyba — robotas padidino produkciją 40%
-
Mažų partijų gamyba — cobotai leido dirbti naktį be operatoriaus
Išvada:
Automatizacija — tai ne prabanga, o protinga investicija. Su UDBU rasite sprendimą savo verslui.
Susisiekite su mumis jau šiandien!
Lazerinis pjovimas ar smūginėmis staklėmis: kuris metodas geriausiai tinka skylėms lakštiniame metale
Lazerinis pjovimas ar smūginėmis staklėmis: kuris metodas geriausiai tinka skylėms lakštiniame metale?
Kai kalbama apie skylių formavimą lakštiniame metale, dažniausiai naudojami du metodai – lazerinis pjovimas ir smūginės (išmušimo) staklės. Abu metodai turi savo privalumų, tačiau tinkamiausio pasirinkimas priklauso nuo kelių veiksnių: medžiagos tipo, skylės dydžio, reikalingo greičio bei tikslumo. Šiame straipsnyje palyginsime abu metodus, kad padėtume jums pasirinkti geriausią variantą jūsų gamybos poreikiams.
Lazerinis pjovimas: tikslumas ir lankstumas
Lazerinis pjovimas naudoja didelės galios lazerio spindulį, kuris išlydo, sudegina arba išgarina medžiagą, taip sukuriant labai tikslius pjūvius ir skyles. Tai itin universalus metodas, leidžiantis išpjauti sudėtingas formas su minimaliu medžiagos deformavimu.
Lazerinio pjovimo privalumai skylėms:
-
Didelis tikslumas: Galima išpjauti itin mažas ir tikslias skyles su siaura tolerancija – idealiai tinka sudėtingiems ar mikro dydžio sprendimams, ypač plonose medžiagose.
-
Nėra įrankių nusidėvėjimo: Skirtingai nei smūginis metodas, lazeris nenaudoja mechaninių įrankių, todėl ilgesnį laiką užtikrina pastovią kokybę be papildomų priežiūros išlaidų.
-
Lankstumas formoms: Galima išpjauti ne tik apvalias, bet ir nestandartines formas (pavyzdžiui, angas, plyšius ar net sudėtingą geometriją), kas suteikia daugiau dizaino laisvės.
-
Mažiau atliekų: Lazeris tiksliai pašalina medžiagą, todėl aplink skylę susidaro mažiau šerpetų nei smūginant.
-
Pritaikomas įvairiems storiams: Lazeriu galima apdirbti tiek plonus, tiek storus lakštus – priklausomai nuo įrangos galios.
Trūkumai:
-
Lėtesnis greitis dideliais kiekiais: Jei reikia greitai išpjauti daug paprastų skylių, lazerinis metodas gali būti lėtesnis nei smūginis.
-
Didesnės eksploatavimo išlaidos: Įranga brangi, taip pat brangesnės elektros sąnaudos, aušinimas ir priežiūra.
-
Šiluminio poveikio zona: Karštis gali paveikti medžiagos savybes aplink skylę – ypač metalams tai aktualu.
Smūginės staklės: greitis ir ekonomiškumas
Smūginis metodas – tai mechaninis procesas, kurio metu presas su štampu jėga išmuša skylę lakštiniame metale. Tai vienas populiariausių būdų, kai reikia paprastų skylių dideliais kiekiais.
Privalumai:
-
Didelis našumas: Greitai formuojamos daugybė skylių, ypač jei skylės yra paprastos formos – puikus pasirinkimas masinei gamybai.
-
Žemesnės eksploatacijos sąnaudos: Palyginti su lazeriu, smūginės staklės naudoja mažiau energijos ir reikalauja paprastesnės priežiūros.
-
Ilgaamžiai įrankiai: Su tinkama priežiūra štampai ir įrankiai tarnauja ilgai, ypač dirbant su vidutinio storio metalais.
-
Ekonomiška paprastoms formoms: Jei reikia daug vienodų, apvalių skylių – tai pigesnis ir greitesnis būdas nei lazerinis pjovimas.
Trūkumai:
-
Formų ribotumas: Sudėtingų ar nestandartinių formų skylės sunkiau išgaunamos, nes reikalauja specialių įrankių – ne tokia lanksti kaip lazerinė sistema.
-
Įrankių dėvėjimasis: Štampai laikui bėgant dėvisi ir juos reikia galąsti arba keisti – tai reiškia papildomas priežiūros išlaidas.
-
Šerpetų susidarymas: Smūgis dažnai palieka šerpetas aplink skylę, ypač storesnėse medžiagose – gali reikėti papildomos apdirbimo operacijos.
-
Storio ribojimai: Nelabai tinka labai plonoms arba labai storoms medžiagoms – geriausiai veikia su vidutinio storio lakštais.
Kurį metodą rinktis?
Rinkitės lazerinį pjovimą, jei:
-
Reikia itin tikslių, sudėtingų ar mažų skylių (pvz., mikro skylės arba nestandartinės formos).
-
Dirbate su įvairaus storio medžiagomis.
-
Jums svarbi mažesnė šiluminio poveikio zona ir minimalūs šerpetai.
-
Užsakymai yra mažo ar vidutinio dydžio, tačiau detalės – sudėtingos.
Rinkitės smūginį metodą, jei:
-
Reikia greitai ir ekonomiškai išmušti daug paprastų skylių (ypač apvalių).
-
Dirbate su storesniais metalo lakštais.
-
Svarbiausias kriterijus – kaina, o šerpetų pašalinimą galite atlikti vėliau.
-
Gamybos apimtis yra didelė ir būtinas aukštas našumas.
Hibridinis metodas
Kai kuriais atvejais geriausias sprendimas – naudoti abu metodus. Šiuolaikinėse gamyklose dažnai naudojamos tiek smūginės staklės, tiek lazeriniai pjovimo įrenginiai, kad kiekvienas gamybos etapas būtų atliekamas efektyviausiai. Pavyzdžiui, smūginėmis staklėmis galima greitai išmušti paprastas skyles, o lazeriu – tikslias ir nestandartines angas toje pačioje detalėje.
Lazeris ar šaltasis pjūklas vamzdžių pjovimui – ką pasirinkti?
Lazeris ar šaltasis pjūklas vamzdžių pjovimui – ką pasirinkti?
Renkantis vamzdžių pjovimo įrangą svarbu atsižvelgti į daugybę veiksnių: tikslumą, greitį, sąnaudas, medžiagų tipą ir kt. Palyginkime dvi populiarias technologijas — lazerinį pjovimą ir šaltąjį pjūklą, kad padėtume jums apsispręsti.
Lazerinis pjovimas
Privalumai:
-
Labai tikslus pjūvis. Lygios briaunos, dažnai nereikia papildomo apdorojimo.
-
Lankstumas. Galima pjauti sudėtingas formas, kiaurymes, kontūrus.
-
Automatizavimas. Šiuolaikiniai lazeriniai įrenginiai lengvai integruojami į gamybos linijas.
Trūkumai:
-
Brangi įranga ir priežiūra.
-
Ribotas efektyvumas su storasieniais vamzdžiais.
-
Reikalingas patyręs operatorius.
Puikiai tinka: aukšto tikslumo darbams, mažoms partijoms, nerūdijančio plieno, aliuminio, vario ir spalvotųjų metalų pjovimui.
Šaltasis pjūklas
Privalumai:
-
Mažesnė kaina. Įranga prieinamesnė.
-
Puikiai tinka storasieniams vamzdžiams.
-
Lengvai naudojamas ir prižiūrimas.
Trūkumai:
-
Tinka tik tiesiam pjūviui.
-
Mažesnis tikslumas. Gali reikėti papildomo apdirbimo.
-
Triukšmingas, daugiau atliekų.
Puikiai tinka: masinei gamybai, geležies metalo vamzdžiams, paprastiems pjūviams.
Palyginimo lentelė:
Rodiklis | Lazerinis pjovimas | Šaltasis pjūklas |
---|---|---|
Tikslumas | Labai aukštas | Vidutinis |
Greitis | Vidutinis | Aukštas (tiesiems pjūviams) |
Įrangos kaina | Aukšta | Vidutinė / žema |
Sudėtingos formos | Taip | Ne |
Priežiūra | Sudėtinga / brangi | Paprasta |
Išvada
Jei jums svarbus tikslumas ir universalumas – rinkitės lazerį. Jei prioritetas – ekonomiškumas ir greitis, rinkitės šaltąjį pjūklą.
Reikia pagalbos renkantis įrangą? Susisiekite su mūsų komanda – padėsime rasti tinkamiausią sprendimą.
CNC tekinimo staklių darbo optimizavimas: patarimai didesniam tikslumui ir efektyvumui
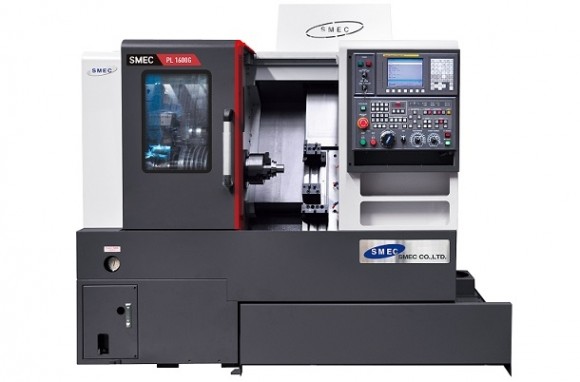
CNC tekinimo staklių darbo optimizavimas: patarimai didesniam tikslumui ir efektyvumui
Šiuolaikinėje gamyboje CNC tekinimo staklės yra nepakeičiama įranga, užtikrinanti didelį tikslumą ir pakartojamumą. Tačiau net ir pažangiausios mašinos reikalauja tinkamos priežiūros, kalibravimo ir darbo organizavimo, kad būtų pasiektas maksimalus našumas. Šiame straipsnyje pateikiame praktinius patarimus, kaip optimizuoti CNC tekinimo staklių darbą, kad pagerintumėte tiek tikslumą, tiek efektyvumą.
1. Reguliari įrangos priežiūra
Tinkama ir periodinė priežiūra yra vienas svarbiausių veiksnių, turinčių įtakos CNC staklių darbui.
-
Tikrinkite tepimo sistemą ir alyvos lygius.
-
Valykite kreipiančiąsias ir darbo paviršius nuo drožlių ir dulkių.
-
Apžiūrėkite velenus ir vežimėlius dėl susidėvėjimo ar vibracijų.
2. Įrankių kalibravimas
Netinkamas įrankio padėties nustatymas gali sukelti gaminio netikslumus.
-
Reguliariai atlikite įrankių kalibravimą.
-
Tikrinkite pjovimo briaunų būklę ir nusidėvėjimą.
-
Patikrinkite automatinio įrankių keitiklio veikimą (jei taikoma).
3. Programinės įrangos ir G-kodo optimizavimas
Efektyvus G-kodas gali sutrumpinti apdorojimo laiką ir sumažinti klaidų riziką.
-
Optimizuokite judėjimo trajektorijas, kad sumažintumėte nereikalingus judesius.
-
Naudokite CAM programinės įrangos optimizavimo funkcijas.
-
Naudokite adaptacinį pjovimą sudėtingiems medžiagų tipams.
4. Ruošinio paruošimas
Netinkamai paruoštas arba netvirtai pritvirtintas ruošinys gali sukelti apdorojimo problemas.
-
Įsitikinkite, kad ruošinys tinkamai pritvirtintas.
-
Naudokite tinkamą tvirtinimo įrangą (griebtuvus, spaustuvus).
-
Patikrinkite ruošinio matmenis ir formą prieš apdirbimą.
5. Duomenų stebėsena ir analizė
Daugelis šiuolaikinių CNC staklių turi veiklos stebėjimo funkcijas, kurios leidžia analizuoti darbo efektyvumą.
-
Naudokite duomenis, kad įvertintumėte ciklo laiką ir įrankių nusidėvėjimą.
-
Nustatykite darbo srauto silpnąsias vietas.
-
Tobulinkite procesą pagal realius veiklos duomenis.
Išvada
CNC tekinimo staklės efektyviai veikia tik tada, kai jos yra tinkamai prižiūrimos ir valdomos. Naudojant kokybiškus įrankius, kruopščiai kalibruojant ir stebint duomenis galima žymiai pagerinti gamybos kokybę, greitį ir patikimumą.
Ieškote naujų ar atnaujintų CNC tekinimo staklių? Peržiūrėkite mūsų pasiūlymus čia
Ką Reikia Žinoti Apie Lazerinį Vamzdžių Pjovimą
Ką Reikia Žinoti Apie Lazerinį Vamzdžių Pjovimą
Lazerinis vamzdžių pjovimas – tai viena pažangiausių šiuolaikinių technologijų, naudojama vamzdinių medžiagų apdirbimui tokiose srityse kaip gamyba, automobilių pramonė, aviacija bei statyba. Šiame procese naudojamas didelės galios lazeris, kuris užtikrina itin tikslų ir greitą pjovimą. Šiame straipsnyje apžvelgsime viską, ką reikia žinoti apie lazerinį vamzdžių pjovimą – kaip jis veikia, kokie jo privalumai, kur dažniausiai taikomas ir kokius aspektus svarbu įvertinti įmonėms, norinčioms diegti šią technologiją.
Kas Yra Lazerinis Vamzdžių Pjovimas?
Lazerinis vamzdžių pjovimas – tai procesas, kurio metu lazerio spindulys naudojamas pjauti metalines ar kitų medžiagų vamzdines konstrukcijas. Lazerio spindulys nukreipiamas į vamzdžio paviršių ir šilumos poveikyje medžiaga yra ištirpdoma arba išgarinama, taip sukuriant švarų bei tikslų pjūvį. Skirtingai nuo tradicinių metodų, tokių kaip pjovimas disku ar perforavimas, lazerinis pjovimas leidžia pasiekti aukščiausią tikslumą bei minimalią atliekų generaciją.
Kaip Veikia Lazerinis Vamzdžių Pjovimas?
Pjovimo procesas dažniausiai vyksta taip:
-
Vamzdžio Paruošimas: Vamzdis įstatomas į įrenginį, dažnai naudojant automatizuotą padavimo sistemą, kuri užtikrina tikslų išlyginimą.
-
Lazerio Įjungimas: Didelės galios lazerio spindulys fokusuojamas naudojant lęšius ar veidrodžius, kad būtų sukurtas koncentruotas šilumos taškas.
-
Pjovimo Procesas: Spindulys kaitina vamzdžio paviršių, kol šis ištirpsta ar išgaruoja, sukuriant precizišką pjūvį.
-
Baigiamasis Apdirbimas: Supjautos detalės surenkamos ir, jei reikia, nukreipiamos tolesniam apdorojimui, pavyzdžiui, šlifavimui ar paviršiaus apdirbimui.
Lazerinio Vamzdžių Pjovimo Privalumai
-
Tikslumas ir precizika: Galima pasiekti itin mažas paklaidas, todėl technologija puikiai tinka sudėtingų formų ir geometrijų gamybai.
-
Universalumas: Veikia su įvairiomis medžiagomis – nerūdijančiu plienu, aliuminiu, anglies plienu ir netgi tokiais egzotiniais metalais kaip titanas.
-
Minimalios atliekos: Pjovimas be fizinio kontakto reiškia mažiau atliekų ir švaresnį procesą.
-
Dizaino laisvė: Galima išpjauti sudėtingus kampus, formas ir konstrukcijas, kurios būtų neįmanomos su tradiciniais metodais.
-
Greitis: Pjovimo procesas gerokai greitesnis nei tradicinės alternatyvos, todėl sumažėja gamybos laikas ir sąnaudos.
-
Automatizavimas: Daugelis šiuolaikinių įrenginių turi automatizuotas tiekimo ir apdirbimo sistemas, kurios padidina efektyvumą ir sumažina žmogiškosios klaidos riziką.
Kur Taikomas Lazerinis Vamzdžių Pjovimas?
Lazerinis vamzdžių pjovimas plačiai naudojamas šiose srityse:
-
Automobilių pramonė: Išmetimo vamzdžių, važiuoklės komponentų, konstrukcinių rėmų gamyba.
-
Aviacija: Detalių gamyba lėktuvams, raketų struktūroms ir kitoms aviacijos sistemoms.
-
Baldų gamyba: Vamzdinių konstrukcijų pjovimas kėdėms, stalams ir kitam dizainui.
-
Statyba: Konstrukciniai rėmai, atramos, plieninės sijos ir pan.
-
Medicinos įranga: Sudėtingos detalės chirurginiams instrumentams ir diagnostikos įrenginiams.
-
Reklama ir menas: Dekoratyviniai elementai, šviesdėžės, ženklai ir meniniai projektai.
Ką Reikia Įvertinti Prieš Diegiant Lazerinio Pjovimo Technologiją?
-
Medžiagos storis: Efektyviausia dirbant su vidutinio storio vamzdžiais. Labai storas medžiagas gali tekti pjauti specialia įranga arba kitais metodais.
-
Vamzdžio geometrija: Tinkama sudėtingoms formoms, tačiau reikia įvertinti įrenginio galimybes apdirbti didelio skersmens ar storio vamzdžius.
-
Įrangos kaina: Pradinis investicijų kaštas gali būti didelis, bet ilgainiui atsiperka per tikslumą, greitį ir mažesnes eksploatacijos sąnaudas.
-
Papildomas apdorojimas: Nors pjūvis švarus, kai kurioms medžiagoms gali reikėti papildomo šlifavimo ar paviršiaus apdirbimo.
-
Lazerio galia: Didesnė galia reiškia greitesnį ir galingesnį pjovimą, bet kartu didesnes energijos sąnaudas.
Kaip Pasirinkti Tinkamą Lazerinio Vamzdžių Pjovimo Sistemą?
Renkantis lazerinę sistemą, svarbu atsižvelgti į:
-
Medžiagų tipus ir storį: Įsitikinkite, kad įrenginys tinka dažniausiai jūsų naudojamoms medžiagoms.
-
Pjovimo greitį ir kokybę: Ieškokite balanso tarp greičio ir precizikos.
-
Automatizavimo galimybes: Jei norite didinti gamybos apimtis, rinkitės sistemą su automatinio padavimo ir detalių išėmimo funkcijomis.
-
Gamintojo aptarnavimą: Svarbu, kad gamintojas teiktų apmokymus, techninę priežiūrą ir programinės įrangos atnaujinimus.
Išvada
Lazerinis vamzdžių pjovimas iš esmės pakeitė požiūrį į vamzdinių komponentų gamybą. Dėl savo tikslumo, greičio ir lankstumo ši technologija yra itin vertinga įvairių sričių gamintojams. Jei jūsų įmonė svarsto apie šios technologijos diegimą, būtina įvertinti pradinius kaštus, tačiau ilgalaikėje perspektyvoje tai gali suteikti esminį konkurencinį pranašumą.
Kaip išsirinkti tinkamiausią CNC programinę įrangą jūsų gamybos poreikiams
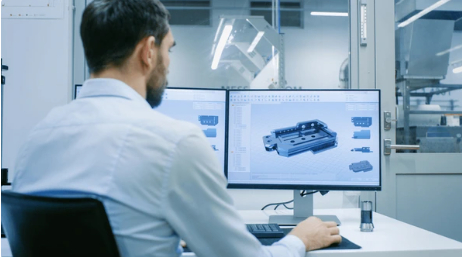
Kaip išsirinkti tinkamiausią CNC programinę įrangą jūsų gamybos poreikiams
CNC (kompiuterinio skaitmeninio valdymo) technologija tapo neatsiejama šiuolaikinės gamybos dalimi. Norint sėkmingai dirbti su CNC įranga, reikia ne tik kokybiškos technikos, bet ir tinkamos programinės įrangos, atitinkančios jūsų specifinius poreikius. Štai kaip išsirinkti tinkamiausią CNC programą:
1. Supraskite savo gamybos poreikius
Prieš rinkdamiesi programą, atsakykite sau:
-
Kokias medžiagas apdorojate (medis, metalas, plastikas ir kt.)
-
Kokio tipo CNC įranga naudojate (frezavimas, lazeris, plazma, tekinimas ir kt.)
-
Koks darbų sudėtingumas (paprasti pjūviai ar sudėtingi 3D modeliai)
-
Kokia jūsų gamybos apimtis (individuali, mažaserijinė ar masinė)
2. Pagrindiniai CNC programinės įrangos tipai
Programos tipas | Funkcija |
---|---|
CAD (kompiuterizuotas projektavimas) | Brėžinių ir dizainų kūrimas |
CAM (kompiuterizuotas gamybos valdymas) | Įrankių trajektorijų generavimas pagal CAD modelius |
G-kodo redaktoriai / simuliatoriai | Kodo peržiūra ir optimizavimas prieš gamybą |
Kai kurios platformos apjungia kelias funkcijas.
3. Populiariausios CNC programos
-
Fusion 360 – CAD ir CAM viename, puikiai tinka prototipų kūrimui
-
SolidWorks + SolidCAM – geras pasirinkimas sudėtingiems 3D apdirbimams
-
Vectric (VCarve, Aspire) – patogi medžio apdirbimui
-
Mach3 / Mach4 – CNC valdymo programos mažoms dirbtuvėms ir hobiams
-
SheetCAM – pritaikyta plazmos, lazerio ir degimo pjovimui
4. Į ką atkreipti dėmesį renkantis?
- Paprastumas naudoti – kaip greitai darbuotojai ją įvaldys
- Suderinamumas – su jūsų CNC įranga
- Pagalba ir dokumentacija – mokymai, techninis palaikymas
- Kaina ir licencijavimas – vienkartinė, prenumerata ar nemokama versija
- Atnaujinimai – ar programa aktyviai palaikoma
5. Ateities perspektyvos: automatizavimas ir debesija
Šiuolaikinės CNC programos dažnai siūlo:
-
Debesų saugyklą dizainams
-
Automatizuotas darbo eigos
-
Integraciją su ERP/logistikos sistemomis
-
Gamybos duomenų analizę
Tai ypač svarbu augantiems verslams.
Išvada
Tinkamai parinkta CNC programinė įranga yra sėkmingos, efektyvios ir pelningos gamybos pagrindas. Nesvarbu, ar esate mėgėjas, ar gamybos profesionalas – tinkama programa padeda maksimaliai išnaudoti įrangos galimybes.