Optimising CNC Lathe Operations: Tips for Enhanced Precision and Efficiency
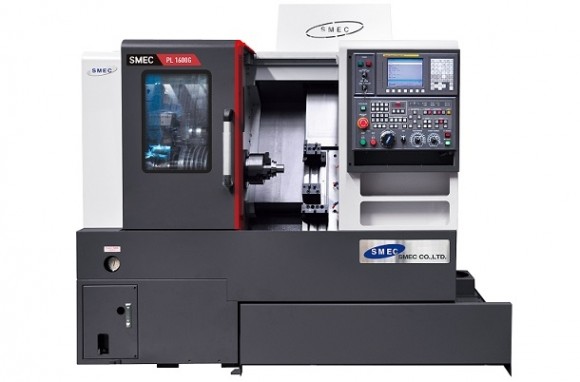
Optimising CNC Lathe Operations: Tips for Enhanced Precision and Efficiency
In modern manufacturing, CNC lathes are essential machines that ensure high precision and repeatability. However, even the most advanced equipment requires proper maintenance, setup, and workflow organisation to reach peak performance. In this article, we share practical tips to help optimise your CNC lathe operations for improved precision and efficiency.
1. Regular Machine Maintenance
Routine maintenance is a critical factor in CNC machine performance.
-
Check lubrication systems and fluid levels.
-
Clean guideways and working surfaces of chips and dust.
-
Inspect spindles and carriages for wear or vibration.
2. Tool Calibration
Incorrect tool positioning can lead to inaccuracies in the final product.
-
Regularly calibrate and reset tools.
-
Check tool edge condition and wear.
-
Inspect automatic tool changers (if applicable).
3. G-Code and Software Optimisation
Efficient G-code programming can significantly reduce cycle times and errors.
-
Review tool paths to eliminate unnecessary movements.
-
Use optimisation features in your CAM software.
-
Implement adaptive cutting for complex materials.
4. Workpiece Preparation
Improperly prepared or clamped workpieces can cause issues during machining.
-
Ensure proper clamping and alignment.
-
Use suitable holders or chucks.
-
Verify the size and shape of the raw material before processing.
5. Monitoring and Data Analysis
Modern CNC machines often include monitoring tools for performance tracking.
-
Use data to evaluate cycle times and tool wear.
-
Identify workflow bottlenecks or inefficiencies.
-
Improve processes based on real-time performance data.
Conclusion
CNC lathes deliver optimal results only when properly maintained and operated. With the right setup, high-quality tools, and consistent monitoring, you can significantly improve your production quality, speed, and reliability.
Looking to upgrade or buy a new CNC lathe? Explore our product selection here